Facility Management für Lagerimmobilien: Effizienz, Sicherheit und Nachhaltigkeit
Facility Management: Lagerimmobilien

Hochregallager Aufbau und Funktionsweise, Verwendung
Wenn man sich vergegenwärtigt, welche Vielfalt schon allein in ihrer Konstruktion Hochregallager besitzen können, ist es besonders wichtig, zunächst einige Grundlagen zu klären. Wenn wir uns über den Betrieb und die Instandhaltung unterhalten wollen, so wird es nicht ausbleiben können das diese Unterschiedlichkeit eine gewisse Rolle spielt und auch berücksichtigt werden muss.
In einem der folgenden Abschnitte werden wir uns mit dem Thema „Prinzipien, Regeln und Gesetze der Lagerwirtschaft“ zu beschäftigen haben. Das ist deshalb notwendig, weil jedes Lager, dass errichtet wird, dem zuvor definierten betrieblichen Bedarf entsprechen muss. Das trifft grundsätzlich zu, also auch auf Hochregallager.
Effiziente Lagerimmobilien für optimale Logistikprozesse
- Allgemeines
- Nutzung
- Konzepte
- Lagermenge
- Überblick
- Bedeutung
- Funktion
- Regalarten
- Technologieeinsatz
- Lagerhaltung
- Vorteile
- Nachteile
- Herausforderungen
Allgemeines: Lagerflächenanalyse für wirtschaftliche Standortentscheidungen
Moderne Planungen sehen also ein Hochregallager nicht als eine Stand-Alone-Einrichtung, sondern vielmehr ein wesentliches Element betrieblicher Produktion. In der Medienwirtschaft würde man ein Lager als Puffergefäß bezeichnen können, also eine Stelle, an der ein sich im Produktionsprozess befindliches Medium zeitweise „aufhält“, um dann wieder abgerufen zu werden zum nächsten Schritt.
Also ist es zunächst wichtig, die Organisation und den Prozess der Produktion zu verstehen um sagen zu können, wo welche „Puffergefäße“ benötigt werden.
Allerdings ist die Planung bei der Lagerwirtschaft insofern sehr komfortabel, als die Zustände des zu transportierenden Gutes nur bedingt eine Rolle spielen, also Drücke, Dichte, Konsistenz, Temperaturen und Ähnliches kaum wichtig sind.
Das stimmt nicht ganz, denn beispielsweise dürfen Temperaturen in einem Lager nicht unter 0 °C fallen, die Ablagestelle für das jeweilige Lagergut muss das Gewicht aushalten können, und ebenso muss der vorhandene Raum an der Lagerstelle groß genug sein, um ein bestimmtes Gut aufnehmen zu können. Aber ein erheblicher Vorteil besteht darin, dass die einzelnen Lagerstellen trotz der genannten Anforderungen nicht zwingend räumlich voneinander getrennt sein müssen.
Dieser Umstand ermöglicht im Prinzip eine völlig ungeordnete Lagerung. So können beispielsweise die Schrauben neben den Schweißelektroden, die Glasscheiben neben den Pumpen usw. gelagert werden, gerade, wie es passt.
Die Herausforderung liegt also einzig darin, exakt zu wissen, wie es gerade passt, also welcher Platz geeignet und frei ist.
Dass hierfür nicht nur die Hardware, wie Gebäude, Regale usw. notwendig ist, sondern auch ein „Gedächtnis“, das weiß, wo was liegt, versteht sich von selbst. Ein Hochregallager maximiert effektiv die vorhandenen Lagerflächen und steigert somit die Lagerkapazität eines Unternehmens. Diese Lagerform ermöglicht eine individuelle Gestaltung in Aufbau, Höhe und Anordnung der Regale, um sie optimal an die spezifischen Gegebenheiten eines Betriebs anzupassen. Hochregallager, definiert durch eine Mindesthöhe von 12 Metern, können in Deutschland bis zu einer gesetzlich geregelten Maximalhöhe von 50 Metern errichtet werden. Sie bestehen aus einer Anordnung von Schwerlastregalen, die als robuste Palettenregale ausgeführt sind. Diese Regale zeichnen sich durch eine hohe Belastbarkeit mit Feldlasten von bis zu 28 Tonnen aus und sind aufgrund ihrer stabilen Stahlkonstruktion und speziellen Oberflächenbeschichtungen sowohl für den Innen- als auch für den Außeneinsatz geeignet. Zur Lagerung kleinerer Güter oder loser Ware werden die Regale mit passenden Lagerbehältern ausgestattet oder um Lösungen für die Kleinteilelagerung ergänzt. In diesem Artikel erfahren Sie mehr über die Vor- und Nachteile von Hochregallagern sowie über die Bauformen, die sich für verschiedene Betriebstypen eignen könnten.
Also ist zunächst ein allgemeiner Überblick nötig, wie das mit der Lagerwirtschaft ist, was es für Varianten gibt und worauf es ankommt.
Einige Beispiele sollen das deutlich machen.
Schwerlastregale
Palettenregale
Lagerbehälter
Kleinteilelagerung.
Hochregallager – Effiziente Lagerlösung für eine logistikintensive Produktion
Ein Hochregallager stellt eine effiziente Lösung dar, um die Logistik in Produktionsbetrieben mit hohem Warendurchlauf zu optimieren. Es ermöglicht auf begrenzter Fläche eine deutlich höhere Lagerkapazität im Vergleich zu traditionellen Lagerkonzepten. Die Struktur dieser Lager nutzt vor allem die vertikale Raumhöhe optimal aus, was eine erhebliche Effizienzsteigerung mit sich bringt. Zudem lassen sich die Prozesse zur Ein- und Auslagerung effizient koordinieren, wodurch sowohl der Arbeitsaufwand als auch die Personalkosten reduziert werden können.
Die modulare und kompakte Bauweise von Hochregallagern erleichtert die Automatisierung des Lagerbetriebs. Viele Hochregallager sind mit fortschrittlichen Lagerverwaltungssystemen ausgestattet, was in Kombination mit einer geeigneten Lagerstrategie ein hohes Optimierungspotenzial bietet. Auch manuelle Bedienung ist insbesondere bei kleineren Anlagen üblich und durchführbar.
Allerdings erfordert die Einrichtung eines Hochregallagers eine umfassende und vorausschauende Planung. Wichtige Aspekte, die vor dem Bau geklärt werden müssen, umfassen die zukünftig benötigten Kapazitäten, die Auswahl der Fördertechnik und die optimale Verbindung der einzelnen Lagerbereiche zur Gewährleistung effizienter Arbeitsabläufe.
Effiziente Nutzung von Raum und Lagerflächen
Hochregallager sind mit hohen Investitionskosten verbunden, die mit steigendem Automatisierungsgrad zunehmen können. Der Aufwand für Organisation und Planung ist groß, und die Konstruktion erfordert eine aufwendige Umsetzung, um die notwendige Stabilität und Belastbarkeit zu sichern. Spezielle Regalbediengeräte sind erforderlich, und die Bedienenden müssen entsprechend geschult werden. Darüber hinaus sind bestehende Hochregallager schwer zu erweitern oder umzubauen, was die Flexibilität einschränkt.
Vor- und Nachteile von Hochregallagern
Vor dem Bau eines Hochregallagers ist es daher essentiell, alle Vor- und Nachteile gründlich zu analysieren und zu bewerten, um mögliche Fehlinvestitionen zu vermeiden. Die Vorzüge, wie die effiziente Nutzung von Raum und Lagerflächen, die Möglichkeit zur Automatisierung von Prozessen, die Flexibilität bezüglich verschiedener Lagerstrategien und die Eignung für unterschiedliche Lagergüter müssen den Herausforderungen, wie hohen Kosten, großem organisatorischen Aufwand und potenziellen Erweiterungsproblemen gegenübergestellt werden.
Zusammenfassende Übersicht Vor- und Nachteile von Hochregallagern
Vor- | Nachteile |
---|---|
Gute Ausnutzung von Raum und Lagerflächen | Hohe Investitionskosten |
Gut geeignet, um Prozesse zu automatisieren | Hoher Aufwand für Organisation und Planung |
Gut und flexibel an die unterschiedliche Lagerstrategien anpassbar | Hoher Statik- Konstruktionsaufwand, um die nötige Belastbarkeit zu gewährleisten |
Geeignet für unterschiedliche Lagergüter | Extra Regalbediengeräte nötig (inkl. Personalschulungen) |
Günstig in Branchen mit hohem Rohstoffbedarf und großer Produktvielfalt | Hochregallager lassen sich nur schwer erweitern oder umbauen |
Effiziente Ein- und Auslagerung | Totalausfall möglich |
Geringere Personalkosten und Arbeitsdauer | Hoher Kontroll- und Wartungsaufwand |
Kosten pro Einheit der Lagerkapazität
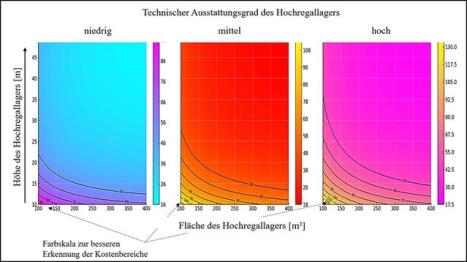
Kosten pro Einheit der Lagerkapazität
Wir können beobachten, dass bestimmte Kombinationen von Höhe und Grundfläche zu einer Minimierung der Kosten pro Lagerkapazität führen. Typischerweise scheint eine höhere Lagerhöhe bei einer moderaten Grundfläche die kosteneffizienteste Option zu sein, was die Annahme bestätigt, dass eine effektive Nutzung des vertikalen Raums die Wirtschaftlichkeit erheblich verbessern kann.

Einfluss des Ausstattungsgrades
Die Grafik zeigt die Kosten pro Einheit der Lagerkapazität in Abhängigkeit von der Grundfläche und der Höhe des Hochregallagers. Die Farbskala (z.B. von violett zu gelb) zeigt an, dass niedrigere Werte (dunklere Töne) wirtschaftlicher sind, während höhere Werte (hellere Töne) weniger wirtschaftlich sind.
Wir haben hier eine allgemeine Analyse erstellt, die das Prinzip darstellt. Diese Analyse könnte weiter verfeinert werden, indem man realistischere Kostenfaktoren oder spezifische Anforderungen eines konkreten Betriebs einbezieht. Auch könnten weitere Faktoren wie die Zugänglichkeit und die Kosten für die Automatisierungstechnik berücksichtigt werden, um eine präzisere Entscheidungshilfe für die Planung von Hochregallagern zu bieten.
Die Sache mit der Automatisierungstechnik haben wir mal gemacht (niedrig, mittel und hoch). Hoch soll bedeuten ein automatisiertes Hochregallager nach dem Prinzip der chaotischen Lagerführung, also die höchste zu erwartende Ausstattung.
Im nächsten Bild wird dieser Zusammenhang deutlich. Das Beispiel zeigt die im vorherigen Bild drei genannten Ausstattungsgrade, steigend von links nach rechts.
Hat man eine Fläche von beispielsweise 200 m² zur Verfügung und setzt Lagerkosten von 50 Einheiten an, so „treibt“ der Ausstattungsgrad das Lager konstruktiv in die Höhe; im Beispiel von 15 m auf ca. 20 m.
Im nächsten Bild wird ein Lager mit sehr hohem Ausstattungsgrad dargestellt. Das Diagramm erlaubt eine Einordnung von verfügbarer Lagerfläche im Zusammenhang mit den zu erwartenden Kosten pro Lagereinheit und der Bauhöhe.
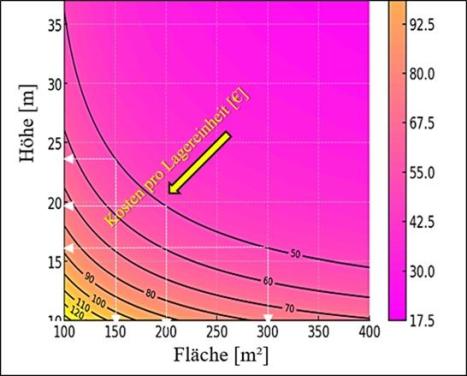
Lager mit hohem Ausstattungsgrad
Die mathematischen Zusammenhänge gestalten sich nach speziell zu berechnenden Kurven, sind also mit einem linearen Ansatz nicht abzuschätzen.
Die Absicht dieser Darstellungen ist es, deutlich zu machen, dass diese Zusammenhänge möglichst konkret bei der Anlagenplanung zu verifizieren sind, um aus den geometrischen Gegebenheiten (Fläche und Höhe sowie technischer Ausstattung) die zu erwartenden Betriebskosten vorherzusagen - zumindest in einem gewissen Genauigkeitskorridor.
Just-in-Time-Konzepte und deren Auswirkungen auf die Lagerhaltung
Damit die Lagerkosten bei Just-in-Time-(JIT)-Konzepten minimal werden, sind folgende Voraussetzungen erforderlich:
Präzise Planung und Steuerung der Lieferkette
Eine wesentliche Randbedingung der Funktion eines Lagers die Lieferung und mithin die Entnahme.
Dabei sind zu berücksichtigen:
Bedarfsprognosen: Exakte und datenbasierte Vorhersagen des Materialbedarfs, um Überbestände oder Engpässe zu vermeiden.
Lieferpläne: Koordinierte und abgestimmte Anlieferzeiten, um Materialien genau dann bereitzustellen, wenn sie benötigt werden.
Qualität und Termintreue: Lieferanten müssen in der Lage sein, Materialien pünktlich und in einwandfreiem Zustand bereitzustellen.
Standortnähe: Lieferanten sollten geografisch nah sein, um Transportzeiten und -kosten zu reduzieren.
Effiziente Logistik und Fördertechnik
Die Konfiguration eines individuellen Lagerregalsystems lässt sich in drei Schritten effektiv durchführen. Zunächst wählt man das Grundregal aus, welches den Basisanforderungen entspricht und passt dieses anschließend an spezifische Bedürfnisse an, indem man die Höhe, Breite und die gewünschte Anzahl an Fachböden sowie die Aussteifung festlegt. Ob für Fachbodenregale, Weitspannregale, Palettenregale, Reifenregale oder andere Lagerlösungen – Verschiedene Unternehmen bieten eine vielfältige Auswahl, um den unterschiedlichsten Lageranforderungen in Werkstätten, Garagen, Lagern oder Logistikzentren gerecht zu werden. Die hohe Qualität der Produkte und das unterstützende Fachwissen der Anbieter tragen dazu bei, Effizienz und Organisation im Lager herzustellen bzw. zu verbessern.
Ergänzend spielt die Fördertechnik, eine Teildisziplin des Maschinenbaus, eine zentrale Rolle in der Logistik und befasst sich mit der Konzeption, Auslegung und Ausführung von Fördermitteln für Stück- oder Schüttgut. Zu den Fördermitteln zählen beispielsweise Krane, Bandförderer und Gabelstapler, die in unterschiedlichen Betriebsbereichen wie Häfen, Flughäfen, Bergbau oder Industriebetrieben zum Einsatz kommen. Die Fördertechnik umfasst nicht nur die technischen Komponenten, sondern auch die Prozessgestaltung bei der Anlagenbedienung, wodurch sie sich von der Verkehrstechnik unterscheidet, die den weiträumigen Transport behandelt.
Innerbetriebliche Transportsysteme, wie Stetigförderer und Unstetigförderer, unterstützen den effizienten Transport von Gütern innerhalb eines Betriebes. Hierzu gehören Rollenbahnen, Gurtbandförderer sowie durch Menschen bediente Flurförderzeuge und automatische LKW-Verladesysteme. Diese Systeme sind darauf ausgerichtet, das Fördergut möglichst effizient von der Aufgabestelle zur Abgabestelle zu befördern. In der Fabrikautomation spielen zudem pneumatische Antriebe eine wichtige Rolle, um Halbfabrikate und Fertigprodukte zu fördern.
Die Kombination aus optimierter Lagerregalkonfiguration und intelligenter Fördertechnik ermöglicht eine Steigerung der Produktivität und Effizienz in modernen Lager- und Produktionsumgebungen.
Optimierte Lagerverwaltung
In modernen Lagerumgebungen spielen automatisierte Hochregallager (HRL) für schwere und mittelschwere Lasten eine zentrale Rolle. Diese Lager werden durch fortschrittliche Softwarelösungen gesteuert, wodurch der Ein- und Auslagerprozess vollkommen autonom abläuft. Diese Systeme bieten eine hohe Dynamik und Sicherheit und sind in erster Linie für den Rund-um-die-Uhr-Betrieb ausgelegt. Ein besonderes Merkmal dieser Lager ist die Silobauweise, bei der das Lagersystem selbst als tragende Struktur für Dach und Fassade dient. Dies eliminiert die Notwendigkeit einer separaten Hallenfassade, was zu erheblichen Einsparungen bei den Baukosten führen kann.
Zur effizienten Steuerung der Materialflüsse werden in solchen Lagern IT-gestützte Systeme eingesetzt, die Lagerverwaltungssysteme (LVS) und Echtzeitdaten nutzen. Diese Technologien ermöglichen es, den Lagerbestand auf ein notwendiges Minimum zu reduzieren und gleichzeitig eine präzise Steuerung des Nachschubs zu gewährleisten. Minimale Sicherheitsbestände und eine optimierte Nachschubsteuerung sind entscheidend für die Reduzierung von Lagerhaltungskosten und die Steigerung der Effizienz in der Lagerlogistik. Diese Ansätze tragen dazu bei, die Gesamtbetriebskosten zu senken, während gleichzeitig die Verfügbarkeit und die Schnelligkeit in der Lieferkette verbessert werden.
An dieser Stelle sollten wir auch einmal darüber nachdenken, was eigentlich alles zu lagern ist. Nehmen wir ein Beispiel: Schrauben und Rohre. Während die Schrauben ohne große Überlegung ins Hochregallager kommen, wird das mit den Rohren problematisch. Die passen dort im Allgemeinen nicht rein. Also wird deutlich, dass bei der Konzipierung eines Hochregallagers auch parallel an all die Lagergüter zu denken ist, die aus unterschiedlichen Gründen anderweitig gelagert werden müssen. Diese Gründe müssen nicht immer die Größe und das Gewicht sein. Auch physikalische oder chemische Anforderungen können eine Lagerung im allgemeinen Hochregallager ausschließen. Weil unser Thema aber Hochregallager heißt, mag es gestattet sein, die ausgeschlossenen Güter hier nicht weiter zu betrachten. Vergessen dürfen sie allerdings keinesfalls werden! Sie müssen auf jeden Fall auch Inhalt des Gesamt-Lagerkonzeptes sein.
Flexibilität in der Produktion – durchgängige Prozesse
Schnelle Umrüstung: Produktionssysteme müssen auf wechselnde Anforderungen schnell reagieren können, um Just-in-Time-Produktion effektiv zu unterstützen.
Puffer für Engpässe: Einrichtung strategischer Puffersysteme für kritische Materialien, um Produktionsausfälle zu vermeiden.
Nahtlose Prozesse in Logistik und Produktion für eine effiziente Steuerung von Material- und Informationsflüssen
Durchgängige Prozesse für Logistik und Produktion umfassen eine integrierte Kette von Aktivitäten, die auf eine effiziente Material- und Informationsflusssteuerung zwischen Anlieferung und Endversand ausgerichtet sind.
Hier eine kurze Erläuterung der einzelnen Schritte:
Anlieferung und Wareneingang: Der Prozess beginnt mit der Annahme der eingehenden Materialien. Die Ware wird geprüft, registriert und für die Einlagerung oder direkte Weiterleitung an die Produktion vorbereitet.
Management-Funktion: Überwacht und koordiniert die verschiedenen logistischen und produktionsbezogenen Aktivitäten. Diese Funktion stellt sicher, dass alle Prozesse effizient ablaufen und Optimierungspotenziale genutzt werden.
Lagerung: Hier werden die Materialien systematisch gelagert. Moderne Lagerverwaltungssysteme optimieren die Lagerhaltung und unterstützen die schnelle Entnahme der Materialien.
Innerbetriebliche Transporte: Bewegen Materialien zwischen verschiedenen Stationen innerhalb des Betriebs, etwa von den Lagern zu den Produktionslinien oder zwischen den Produktionsstätten.
Produktionsversorgung: Umfasst die rechtzeitige Bereitstellung aller benötigten Materialien an den Produktionslinien, um einen störungsfreien Produktionsablauf zu gewährleisten.
Lagerleitstand: Eine zentrale Steuerungseinheit, die die Übersicht und Kontrolle über alle Lagerprozesse behält, von der Einlagerung bis zur Auslagerung.
Kommissionierung: Hier werden die für Aufträge benötigten Artikel aus dem Lager geholt und für die Weiterverarbeitung oder den Versand vorbereitet.
Verpackung und Versand: Die fertigen Produkte werden sicher verpackt und für den Transport vorbereitet. Dies schließt auch das Erstellen von Versanddokumenten ein.
Transport: Der letzte Schritt umfasst den Transport der fertigen Produkte zum Kunden oder zum nächsten Vertriebszentrum. Dieser Schritt ist entscheidend für die Einhaltung der Lieferzeiten und die Kundenzufriedenheit.
Durch Verwendung digitaler Plattformen erfolgt die Integration von Technologien, wie
Blockchain oder
Cloud-Systemen
Risikomanagement
Alternative Lieferanten: Aufbau eines Netzwerks aus alternativen Lieferquellen zur Absicherung gegen Lieferausfälle.
Notfallpläne: Definition von Strategien zur Bewältigung unvorhergesehener Ereignisse, wie Lieferverzögerungen oder Nachfrageschwankungen.
Durch die Erfüllung dieser Voraussetzungen können Lagerkosten signifikant gesenkt werden, da unnötige Lagerhaltung vermieden wird, Materialflüsse optimiert sind und eine hohe Transparenz in der Supply Chain herrscht. JIT 3 ermöglicht somit eine schlanke, kostenoptimierte Lagerhaltung bei gleichzeitiger Flexibilität.
Die sichere Nutzung von Fördermitteln in Lagerumgebungen erfordert die Einrichtung sicherer Arbeitsbedingungen, basierend auf einer gründlichen Risikoanalyse, um Beschädigungen der Lagereinrichtungen und die Gefährdung der Gesundheit zu minimieren. Eine Schlüsselrolle spielen dabei Mitarbeiterschulungen und die Vermeidung von Arbeitsbedingungen, die zu erhöhten Risiken führen könnten.
Es ist zudem wichtig, eine Reihe von Sicherheitsmaßnahmen zu berücksichtigen:
Einhaltung von Vorschriften: Die nationalen und örtlichen Vorschriften, wie Brandsicherheitsbestimmungen, müssen stets eingehalten werden.
Schulung des Personals: Mitarbeiter, die Fördermittel nutzen, müssen geschult sein, um die Tragfähigkeit der Regale zu verstehen und sicher zu bedienen.
Übereinstimmung der Umgebung mit der Spezifikation: Die Umgebung muss trocken und sauber sein, und es muss sichergestellt werden, dass Standortbedingungen wie Wind und Wetter berücksichtigt werden, die die Qualität und Haltbarkeit von Oberflächenbehandlungen beeinflussen können.
Spezifikationen der Ladeeinheiten:
Die Außenmaße der Ladeeinheiten dürfen die spezifizierten Grenzen nicht überschreiten, um Kollisionen zu vermeiden.
Das Gewicht der Ladeeinheiten darf die spezifizierten Grenzen nicht überschreiten, um die max. Belastung nicht zu überschreiten. Bei der Beladung von Regalen ist zu beachten, dass bei der statischen Berechnung von einer Streckenlast ausgegangen wird. Das bedeutet, dass eine Punktbelastung zu reduzieren ist.
Eignung des Fördermittels: Es muss gewährleistet sein, dass z.B. der Wendekreis des Gabelstaplers die spezifizierten Gangbreiten nicht überschreitet, um sicheres Manövrieren zu ermöglichen.
Kompatibilität und Zustand der Ladehilfsmittel: Diese müssen den Spezifikationen entsprechen und in gutem Zustand sein. Die Stabilität der auf Paletten gelagerten Waren muss innerhalb der vereinbarten Toleranzen liegen.
Ordnung und Sauberkeit: Diese sind im Bereich der Staplerarbeitsgänge kritisch, um Hindernisse zu vermeiden.
Nutzung gemäß Vertragsspezifikation: Die Lagereinrichtungen müssen entsprechend den gelieferten Spezifikationen verwendet werden.
Auswirkungen von Veränderungen: Jegliche Modifikation der Lagereinrichtung kann deren Sicherheit beeinflussen.
Lagerverwaltungssystem: Dieses sollte die Berechnung unterschiedlicher Belastungenermöglichen.
Fachgerechte Montage: Wenn die Montage durch den Benutzer oder Subunternehmer erfolgt, muss sie gemäß der Anleitung des Herstellers durchgeführt werden.
Eigenschaften des Regalfundaments: Es muss ausreichend Widerstand und Steifigkeit für die zu tragenden Lasten bieten.
Berechnung externer Lasten: Der Standort muss für die Berechnung von Wind-, Schnee-und Erdbebenlasten geeignet sein.
Heizung und Beleuchtung: Diese müssen im Lagerbereich angemessen sein.
Stützenschutz und Inspektionen: Diese sind erforderlich und sollten regelmäßig durchgeführt werden, um Schäden sofort zu erkennen und zu beheben.
Lagermenge und Schnittstelle zur Beschaffung
Hochregallager sind hochentwickelte Lagerstrukturen, die darauf ausgelegt sind, die verfügbare Lagerfläche maximal auszunutzen, indem sie in die Höhe statt in die Breite bauen. Hierbei wird eine Vielzahl von Regalarten und Bauweisen genutzt, die auf die spezifischen Anforderungen des Lagerguts und der Logistikprozesse abgestimmt sind. Im Folgenden werden die unterschiedlichen Bauweisen und Regalarten von Hochregallagern erläutert.
Bedeutung moderner Lagerhaltung
Moderne Lagerhaltung spielt eine zentrale Rolle in der heutigen Wirtschaft und Logistik, da sie die Effizienz, Flexibilität und Kosteneffektivität von Unternehmen maßgeblich beeinflusst. Mit fortschrittlichen Technologien wie Automatisierung, Echtzeit-Datenanalyse und künstlicher Intelligenz können optimale Lagerprozesse geplant, bzw. vorhandene optimiert werden, um eine schnelle Reaktionsfähigkeit auf Marktveränderungen und Kundenanforderungen zu gewährleisten. Zudem ermöglicht eine gut organisierte Lagerhaltung eine präzise Bestandsführung, wodurch Überbestände und Lieferengpässe vermieden werden. Dies trägt nicht nur zur Senkung von Lagerkosten bei, sondern verbessert auch die Liefergeschwindigkeit und -zuverlässigkeit. Ein weiteres wichtiges Element ist die Nachhaltigkeit, da moderne Lagerhaltung durch effiziente Nutzung von Ressourcen und optimierte Lieferketten einen Beitrag zur Reduktion von Umweltbelastungen leisten kann. Insgesamt ist die moderne Lagerhaltung ein entscheidender Faktor, um Wettbewerbsfähigkeit und Kundenzufriedenheit sicherzustellen.
Planung der Lagereinrichtungen
Um eine präzise und sichere Auslegung sowie Tragfähigkeitsbemessung für Lagereinrichtungen zu gewährleisten, sind detaillierte Informationen von essentieller Bedeutung. Diese sollten umfassend vom Benutzer bereitgestellt werden, um den Anforderungen der Normen EN 15629 und EN 15620 gerecht zu werden.
Folgende Details sind dabei von besonderer Relevanz:
Details des Gebäudes und der Umgebung: Es müssen genaue Angaben zum Gebäude, in dem die Lagereinrichtung installiert werden soll, einschließlich der spezifischenUmgebungsbedingungen, gemacht werden. Diese Informationen beeinflussen Entscheidungen bezüglich der Materialauswahl und der Konstruktionsweise der Lagerlösung.
Eigenschaften des Fundaments und des Bodens: Die Tragfähigkeit und Stabilität des Fundaments sowie die Beschaffenheit des Bodens sind entscheidend für die Planung. Sie bestimmen, welche Lagerlösungen realisierbar sind und welche Sicherheitsvorkehrungen getroffen werden müssen.
Details der zu lagernden Waren: Vollständige Informationen über die Art der Waren, die gelagert werden sollen, einschließlich der Spezifikationen von Paletten oder anderen Ladehilfsmitteln, sind notwendig. Diese Details sind entscheidend für die Gestaltung der Lagerkapazität und die Auswahl des geeigneten Lagersystems.
Zulässige Belastungen: Angaben über die maximalen Lasten, die die Lagereinrichtungen tragen können, sind erforderlich, um die Sicherheit und Funktionalität der Lagerstrukturen sicherzustellen.
Geplante Auslegung der Einrichtung: Die geplante Konfiguration der Lagereinrichtung muss ausreichende Bemessungsfreiräume für die sichere Ein- und Auslagerung von Waren ermöglichen, abgestimmt auf die erwartete Durchsatzleistung.
Spezifikationen der Fördermittel: Detaillierte Informationen über die zu verwendenden Fördermittel, wie z.B. Staplertypen, sind erforderlich. Diese müssen auf die Lagerstruktur abgestimmt sein, um effektive Gangbreiten und Wenderadien sicherzustellen.
Stoßwiderstand und Kollisionsvermeidung: Es müssen Anforderungen an die Stoßfestigkeit der Lagereinrichtungen festgelegt werden, um Schäden durch Unfälle oder Kollisionen zu minimieren.
Verantwortlichkeit für die Montage: Klare Vereinbarungen darüber, wer die Montage der Lagereinrichtungen durchführt, sind notwendig, um eine fachgerechte Installation zu garantieren.
Informationen zu künftigen Änderungen: Alle bekannten Informationen über geplante Änderungen in den Lageranforderungen müssen im Voraus berücksichtigt werden, um zukünftige Anpassungen zu erleichtern und zusätzliche Kosten zu vermeiden.
Die Bereitstellung dieser detaillierten Informationen ermöglicht eine optimierte Planung und Ausführung der Lagereinrichtung, die sowohl den aktuellen als auch den zukünftigen Anforderungen entspricht. Einbeziehung periphärer Gewerke unter Berücksichtigung des späteren Betriebs Das Hochregallager allein wird nicht ohne begleitende Gewerke und Leistungen erfolgreich arbeiten. Man sollte bei der Planung davon ausgehen, dass es sich quasi um ein eigenständiges Gebäude handelt, welches eine Reihe von Unterstützungen benötigt.
Was hiermit gemeint ist sollen folgende Stichworte andeuten:
Bewachung
Heizung/Kühlung/Lüftung
An- und Abtransport
Reinigung
Einrichtungen für die Verwaltung (Büro, Sanitär)
Beleuchtung
Brandschutz.
Die Liste ließe sich fortsetzen, je nachdem, was benötigt wird. Auf jeden Fall wird klar, das bei der Planung nichts vergessen werden darf. Entscheidend sind klare Schnittstellen
zum Kerngeschäft und
zum „übrigen“ Facility Management des Unternehmens.
Konstruktion und Montage der Lagereinrichtung
Die Errichtung der Lagereinrichtungen erfolgt streng nach den Spezifikationen, technischen Zeichnungen und Montageanleitungen des Herstellers, um deren Stabilität und Betriebssicherheit zu gewährleisten. Eine korrekte Montage ist entscheidend, da nur so die strukturelle Integrität und die vorgesehene Funktionssicherheit der Einrichtung garantiert werden können. Insbesondere wenn die Endmontage durch den Anwender selbst stattfindet, ist die strikte Einhaltung der Herstellervorgaben essentiell.
Abweichungen von diesen Anleitungen können zu erheblichen Sicherheitsrisiken führen.
Technische Anforderungen an die Tragfähigkeit: Die Berechnung der Tragfähigkeit der Lagereinrichtungen basiert auf der Annahme, dass alle Ladevorgänge gemäß der anerkannten fachlichen Praxis durchgeführt werden. Dabei spielt auch die Beschaffenheit des Lagerbodens eine wesentliche Rolle. Der Boden muss die erforderliche Tragfähigkeit und Steifigkeit aufweisen, um sowohl das Gewicht des Regalsystems als auch der gelagerten Güter sicher tragen zu können. Eine gleichmäßige Oberflächenbeschaffenheit und Planheit des Bodens sind zudem unerlässlich, um eine reibungslose Nutzung von Fördermitteln wie Gabelstaplern und Regalbediengeräten zu ermöglichen.
Belastungsrichtlinien und Sicherheitskennzeichnungen: Es ist die Verantwortung des Herstellers, den Nutzern eine umfassende Anleitung über die maximal zulässigen Belastungen der Regale bereitzustellen. Diese Anleitung sollte präzise Belastungsdaten enthalten und muss an der Lagereinrichtung selbst oder in deren unmittelbarer Nähe deutlich sichtbar angebracht werden.
So wird sichergestellt, dass das Lagerpersonal stets über die Belastungsgrenzen informiert ist und hilft, die Einhaltung dieser Grenzen zu überwachen und mögliche Überbelastungen zu verhindern. Voraussetzend hierfür sind auch die entsprechenden Angaben des Lagergutes. So wird es wahrscheinlich sein, dass es im Hochregallager bereits von der Planung an unterschiedliche Bereiche geben kann, die auf die Eigenschaften des Lagergutes abgestimmt sein müssen.
Überblick über Lagerkonzepte und -Systeme
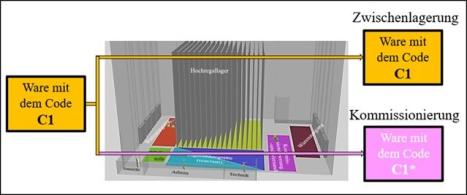
Prinzip der Aufgaben eines Hochregallager
Lagerkonzepte sind strategische Ansätze zur Organisation und Verwaltung von Lagerprozessen, die den individuellen Anforderungen eines Unternehmens angepasst werden. Sie umfassen unterschiedliche Methoden und Strukturen, um Lagerflächen effizient zu nutzen, Bestände optimal zu verwalten und logistische Abläufe zu verbessern. Zu den zentralen Konzepten gehören das Just- in-Time-Lager, das sich durch minimale Bestände und bedarfsgerechte Nachlieferungen auszeichnet, sowie das Pufferlager, das Schwankungen in der Nachfrage ausgleicht. Weitere Ansätze sind das Konsignationslager, bei dem der Lieferant Waren vorfinanziert, und das Cross- Docking, das eine direkte Umladung von Waren ermöglicht, ohne diese zwischenzulagern. Diese Konzepte dienen als Grundlage, um Logistikprozesse flexibel, kosteneffizient und ressourcenschonend zu gestalten und werden im Folgenden detailliert erläutert.
Es sind im Prinzip zwei Aufgaben
eine konkrete Ware zwischen zu lagern und
verschiedene Waren zusammen zu fügen, ohne jedoch ihre Eigenschaften zu verändern.
Im Falle der Zwischenlagerung dient das Lager als „Puffer“. Die Gründe hierfür können sein:
Bildung eines Vorrats, um bei Bedarf sofort Zugriff zu haben
Gewährleistung einer Aufbewahrungssicherheit.
Im zweiten Fall geht es
ebenfalls um das Prinzip der Zwischenlagerung, jedoch
zum Zwecke der Kommissionierung.
Die Ware benötigt im ersten Fall keinen neuen Code, weil an ihr keine Eigenschaften usw. verändert wurden. C1 à C1 Im zweiten Falle wird die Ware zwar bezüglich ihrer Eigenschaften ebenfalls nicht verändert (das geschieht ja in einem Lager prinzipiell nie), jedoch bedarf es eines neuen Codes bei der Auslieferung. C1 à C1*. Wobei man sich unter C1* mehrere, zu einem „Paket“ zusammengefügte Cn vorstellen muss.
Die Veränderung der Eigenschaften der jeweiligen Ware kann nur über einen Prozess (Produktion) erfolgen. Wenn es der Prozess der Produktion vorsieht, dass die produzierte Ware wiederum das Hochregallager anlaufen soll, würde es den Wareneingang erreichen, einen neuen Code haben (zum Beispiel C1**) und ebenso wie ursprünglich die Ware mit dem Code C 1 entsprechend der prozessualen Vorgaben das Lager durchlaufen und verlassen. So gesehen, ist das Prinzip der Lagerung denkbar einfach, denn es geht um nichts anderes, als einen Code zu identifizieren und ihn, nebst dem, was an ihm „dranhängt“ durch das Lager und wieder hinaus zu lavieren. Dieses schlichte Prinzip ist bis zum heutigen Tage so weit entwickelt, dass der Mensch nur noch planend (Bau), ggf. regulierend (Abläufe) und schlimmstenfalls reagierend (Störungen) mitwirken muss.
Bei der Nutzung und Konstruktion der hierfür nötigen Regalbediengeräte in Hochregallagern spielt die Norm FEM 9.831 eine wichtige Rolle. Sie definiert spezifische Toleranzen, Verformungen und Freimaße, die für den sicheren und effizienten Betrieb dieser Geräte erforderlich sind. Die Norm richtet sich an Hochregallager, deren Regalbediengeräte auf Schienen fahren, durch Schienen gestützt werden, mechanisch Lasten aufnehmen und für den Umschlag von Paletten oder ähnlichen Ladehilfsmitteln wie Gitterboxen geeignet sind.
Entstehung und Bedeutung der Norm FEM 9.831
Die Entwicklung der FEM 9.831 wurde initiiert, um sicherzustellen, dass die Bestandteile von Regalbediengeräten den notwendigen Herstellungs-, Montage- und Verformungstoleranzen entsprechen. Diese Toleranzen sind kritisch, um die Funktionssicherheit im Hochregallager zu gewährleisten und gleichzeitig den verfügbaren Raum optimal zu nutzen. Zu große Freimaße könnten zu einer ineffizienten Raumausnutzung und damit zu einer Verschwendung von wertvollem Lagerplatz führen.
Ziele und Anwendungsbereich der Norm: Das Hauptziel der FEM 9.831 ist es, durch die Festlegung von Toleranzen und Verformungen die Funktionssicherheit zu garantieren, ohne die Wirtschaftlichkeit von Dimensionierung, Fertigung und Montage zu beeinträchtigen.
Folgende Bestandteile eines Hochregallagers werden durch die Norm abgedeckt:
Bodenplatte
Fahrschiene
Führungsschiene
Ladeeinheit
Profilkontrolle
Bereitstellplatz (Zentrierung)
Regalbediengerät
Regalkonstruktion.
In der Praxis unterstützt am besten eine spezielle Software die Einhaltung der FEM 9.831, wobei diese je nach Aufgabe interdisziplinäre und maßgeschneiderte Lösungen enthalten sollte, die den Anforderungen der Norm gerecht werden und gleichzeitig effizient und benutzerfreundlich sind. Diese sorgfältige Beachtung der Norm FEM 9.831 stellt sicher, dass alle Komponenten des Hochregallagers nicht nur funktional und sicher sind, sondern auch eine optimale Raumausnutzung ermöglichen.
In manuellen Lagersystemen spielen Paletten und anderes lasttragendes Zubehör eine zentrale Rolle für den sicheren Betrieb und die effiziente Lagerung. Um die Sicherheit und Funktionalität dieser Systeme zu gewährleisten, müssen spezifische Anforderungen an Paletten und Ladehilfsmittel erfüllt werden.
Es geht hier mit FEM 9.831 also beispielhaft um eine der speziellen Normen für Hochregallager. Wie alle Normen ist auch sie sehr spezifisch in ihrer Fachlichkeit, also für die Fachleute gemacht. Damit kann und soll unser Anwendungsdokument auch nicht den Anspruch haben, tief in diese Fachlichkeit einzudringen. Um aber dem Anwender eine kleine Vorstellung zu vermitteln, um was es bei der Planung von Hochregallagern unter anderem auch geht und was zwingend zu beachten ist, wollen wir einmal einige wenige Details aus dieser Norm beispielhaft aufzeigen:
Einige Planungsaspekte für Hochregallager
Fußbodenanforderungen Toleranzen: Die Ebenheit des Hallenbodens ist kritisch für die Funktionalität von Regalanlagen. Gemäß DIN 18202 Tabelle 3 Zeile 3 müssen bestimmte Ebenheitsanforderungen erfüllt sein. Zusätzliche Spezifikationen gemäß DIN EN 15620 sind ebenfalls zu beachten.
Unterfütterung: Für Palettenregal-Ständerwerke ist eine Unterfütterung bis zu 10 mm möglich. Gelochte Unterlegplatten bis 3 mm sind standardmäßig im Lieferumfang enthalten.
Durchbiegung: Die Durchbiegung des Bodens kann die Funktion der Regalanlage beeinträchtigen. Bei größeren Toleranzabweichungen ist eine Rücksprache erforderlich, um die Dübel- oder Verankerungen statisch zu prüfen.
Betongüte und Stärke
Anforderungen: Eine Mindestbetongüte von C20/25 mit adäquater Bewehrung (nach DIN EN 206-1 / DIN 1045-2) und eine Mindestdicke von 20 cm sind erforderlich.
Fachliche Einschätzung: Bei Nichteinhaltung dieser Spezifikationen muss ein Sachverständiger die Bodenverhältnisse beurteilen. Unerwartete Mehraufwendungen fallen nicht unter das Standardangebot.
Verankerung
Bodendübel: Diese müssen im bewehrten Beton verankert werden. Spezialdübel oder chemische Klebeanker sind sinnvoll, aber auch teurer.
Kosten: Mehrkosten können entstehen durch Mehraufwand und erhöhten Bohrerverschleiß, insbesondere wenn Bewehrungsdurchmesser über 8mm liegen oder Bewehrungsstäbe übereinander verlegt sind.
Korrosionsschutz
Magnesithaltige Fußböden: Um Korrosionsbildung zu verhindern, ist eine physikalische Trennung zwischen Fußplatte und Boden notwendig. Geeignete Trennsysteme sind verfügbar, deren Kosten üblicherweise nicht im Standardangebot enthalten sind und zusätzlich zu berücksichtigen sind.
Genehmigungsprozesse
Regulatorische Anforderungen: Die behördlichen Vorschriften und Genehmigungen variieren je nach Bundesland und müssen vom Auftraggeber der Anlage eigenverantwortlich im Rahmen der Genehmigungsplanung eingeholt werden.
Änderungen nach Auftragserteilung
Sollten Änderungen am Gewerk nach Auftragserteilung notwendig werden, erfolgt üblicherweise eine gesonderte Berechnung durch den Auftragnehmer und. Lieferverzögerungen, die daraus resultieren, gehen zu Lasten des Auftraggebers.
Diese Informationen sollen eine Übersicht über einige wichtige Aspekte der Planung und des Betriebs von Hochregallagern bieten, wie sie in der Norm FEM 9.831 festgelegt sind. Sie dienen dazu, dem Anwender eine Vorstellung der komplexen Anforderungen zu vermitteln, die bei der Planung und Realisierung solcher Systeme zu beachten sind, denn alles, was nicht ausreichend berücksichtigt wurde, geht vertragsüblich zulasten des Auftraggebers.
Palettenkonstruktion, Beladung und Kapazität von Paletten
Es ist sicherzustellen, dass die Beladung der Palette deren Nennlast nicht übersteigt. Überladene Paletten können die Stabilität des Lagerregalsystems gefährden und die Sicherheit beeinträchtigen.
Anforderungen an die Palettenkonstruktion und -qualität: Die
Art,
Maße,
Toleranzen,
Qualität und
Konstruktion
der Paletten müssen genau auf die Anforderungen der jeweiligen Lagereinrichtung abgestimmt sein. Beschädigte Paletten oder solche, die den Spezifikationen nicht entsprechen, dürfen nicht verwendet werden. Dies gilt insbesondere für Einfahr- und Durchlaufregalsysteme, die besonders empfindlich hinsichtlich der Palettenqualität sind. Eine unzureichende Palettenqualität kann zu erheblichen Sicherheitsrisiken führen. Beispielsweise darf die Durchbiegung einer korrekt beladenen Palette bei einer Spannbreite, die dem lichten Nennmaß zwischen den Auflageschienen eines Einfahrregals entspricht, 25 mm nicht überschreiten.
Diese Richtlinien gewährleisten, dass manuelle Lagerungssysteme sicher und effizient genutzt werden können, und minimieren das Risiko von Unfällen oder Beschädigungen an der Lagereinrichtung.
Gefahren durch beschädigte Paletten: Beschädigte Paletten können nicht nur die Sicherheit der unmittelbar damit hantierenden Personen gefährden, sondern auch zu schwerwiegenden Beschädigungen der Lagereinrichtung führen. Ein Versagen der Paletten, insbesondere in höheren Ebenen des Regalsystems, stellt ein signifikantes Risiko dar.
Empfehlungen und Spezialanforderungen: Für spezielle Ladehilfsmittel und Lasten, wie Stahlpaletten mit Füßen, sind zusätzliche Vorkehrungen wie Palettenfußauflagen erforderlich. Auch Sonderlasten wie Stahlfässer, Drahtrollen oder andere schwer zu lagernde Objekte müssen durch geeignetes Zubehör, das idealerweise vom ursprünglichen Lieferanten der Lagereinrichtung bereitgestellt wird, unterstützt werden. Empfehlungen zu geeigneten Palettentypen sind bei den potenziellen Lieferanten erhältlich und sollten vor der Anschaffung eingeholt werden.
Auswahl geeigneter Fördermittel
Die verwendeten Gabelstapler oder andere Fördermittel müssen mit der Regalkonstruktion sowie dem Hallenboden kompatibel sein. Sie müssen zudem für eine sichere Ein- und Auslagerung der Waren geeignet sein. Besonderes Augenmerk ist dabei auf die Gangbreite und den Wendekreis der Stapler zu legen. Diese Parameter müssen mit den Gesamtmaßen der Ladeeinheit übereinstimmen.
Schutz vor Beschädigungen durch Fördermittel
Während des normalen Betriebs ist sicherzustellen, dass die Fördermittel entsprechend den Anweisungen des jeweiligen Herstellers eingesetzt werden. Dadurch können Schäden an der Lagereinrichtung vermieden werden. Das Design der Lagereinrichtung berücksichtigt nur die Belastungen und Kräfte, die durch sorgfältige und korrekte Nutzung entstehen. Zusätzliche Einwirkungen, wie Stöße oder Zusammenstöße, sind nur dann berücksichtigt, wenn die Spezifikationen explizit Stoßresistenz fordern.
Durch die Einhaltung dieser Anforderungen wird nicht nur die Betriebssicherheit gewährleistet, sondern auch die Lebensdauer der Lagereinrichtung verlängert und das Unfallrisiko minimiert. Betreiber von Hochregallagern sollten regelmäßig prüfen, ob alle genannten Punkte eingehalten werden, und bei Bedarf Schulungen sowie Wartungsmaßnahmen durchführen.
Die Ladeeinheit
In der Lagerlogistik ist es entscheidend, dass die Handhabung von Ladeeinheiten präzise und sicher erfolgt, um die Integrität der Ware und der Lagereinrichtung zu gewährleisten.
Es folgt eine detaillierte Erläuterung wichtiger Aspekte der Lagerung und Handhabung von Ladeeinheiten.
Gewichtsbeschränkungen: Die Belastung der Lagereinrichtungen muss strikt den vom Planer festgelegten Gewichtsvorgaben entsprechen. Eine Überlastung durch schwerere Ladeeinheiten als vorgegeben, kann die Sicherheit des Lagerbetriebs gefährden und ist nicht zulässig.
Stabilität der Ladeeinheiten: Es ist sicherzustellen, dass die Waren so gestapelt oder auf Paletten arrangiert werden, dass sie während der Lagerung und des Transports stabilbleiben. Instabile Stapelungen können zu Schäden an der Ware und zu Unfällen führen.
Freiraumregelungen: Die physischen Dimensionen der Ladeeinheiten müssen so gewählt werden, dass sie die für den sicheren Betrieb vorgesehenen Freiräume nicht beeinträchtigen. Dies ist entscheidend, um die reibungslose Funktion der Fördermittel und die Sicherheit des Personals zu gewährleisten.
Sachgerechtes Absetzen von Lasten: Die Ein- und Auslagerung von Ladehilfsmitteln muss durch geschultes Personal mit dem richtigen Fördermittel sorgfältig durchgeführt werden. Dabei ist die Übereinstimmung mit den in der Spezifikation angegebenen Lasten zu überprüfen. Ungenaues Platzieren der Paletten kann Beschädigungen an der Lagereinrichtung verursachen.
Vermeidung von Schäden an Lagereinrichtungen: Förderzeuge müssen vorsichtig geführt werden und nur die festgelegten Ladeeinheiten transportieren. Jegliche Schäden, die während des Betriebs auftreten, müssen sofort dem Sicherheitsbeauftragten gemeldet werden.
Einsatz von Holzpaletten: Beim Einsatz von Holzpaletten ist darauf zu achten, dass die tragenden Elemente der Palette den Raum zwischen den Auflageschienen oder Trägern effektiv überbrücken. Die Paletten müssen an den Klötzen unterstützt werden, um ein Brechen der unteren Kufen und somit ein Zusammenbrechen der Palette zu verhindern.
Diese Praktiken sind essentiell, um die Sicherheit und Effizienz in der Lagerung und Handhabung von Ladeeinheiten zu gewährleisten. Durch die Einhaltung dieser Richtlinien können Unfälle vermieden, die Lebensdauer der Lagereinrichtungen verlängert und die allgemeine Betriebssicherheit verbessert werden.
Automatisierte Systeme
Ein automatisches Hochregallager zeichnet sich durch eine besonders effiziente Raumnutzung und hohe Automatisierungsgrade aus. Die Struktur dieser Lager besteht aus Palettenregalen, die zwischen 12 und 45 Meter hoch sein können und sowohl aus Stahl als auch aus Holz gefertigt werden. Zwischen den Regalreihen navigieren Regalbediengeräte (RBG) oder Shuttle-Fahrzeuge selbstständig, um palettierte Waren aufzunehmen oder abzulegen.
Die Konstruktion dieser Lager ist darauf ausgelegt, Platz zu maximieren und Paletten bis zu einem Gewicht von 3.500 kg entweder einfach- oder mehrfachtief zu lagern. Durch diese Kompaktheit wird der verfügbare Lagerplatz optimal genutzt. Darüber hinaus ist die verwendete Technologie sehr robust und funktioniert zuverlässig in einem weiten Temperaturbereich von -30 °C bis +45 °C, was die Lagerlösungen für eine Vielzahl von Branchen geeignet macht. Die fortschrittliche Automatisierung eines solchen Lagers umfasst die selbständige Zuweisung von Regalplätzen basierend auf den Dimensionen der Artikel, was eine optimale Ausnutzung jedes einzelnen Regalfachs ermöglicht. Die Regalbediengeräte arbeiten vollautomatisch, bewegen sich autonom durch die Gänge und übernehmen sowohl das Ablegen als auch das Aufnehmen der Waren. Diese hohe Automatisierung führt zu einer signifikanten Steigerung der Effizienz und Produktivität im Lagerbetrieb.
Hybride Systeme
Hochregallager sind Lagerungssysteme, die effizienten Raumgebrauch ermöglichen, indem sie die vertikale Dimension maximieren. Diese Lager können in verschiedene Systemtypen unterteilt werden, einschließlich automatisierter Systeme, manueller Systeme und hybrider Systeme. Hier konzentrieren wir uns auf das hybride System, das eine Kombination aus automatisierten und manuellen Funktionen bietet.
Ein hybrides Hochregallager kombiniert die Elemente der Automatisierung mit der Flexibilität manueller Eingriffe. Solche Systeme nutzen oft automatisierte Geräte wie Förderbänder, Regalbediengeräte oder automatisierte Transportmittel für den Hauptteil des Lagerbetriebs, bieten jedoch auch die Möglichkeit für manuelles Eingreifen. Dies kann beispielsweise für spezielle Lageraufgaben, Wartungsarbeiten oder in Situationen, wo die Automatisierung an ihre Grenzen stößt, nötig sein.
Vor- und Nachteile hybrider Systeme
Um die Vor- und Nachteile eines hybriden Hochregallagers besser darzustellen, sind diese in einer Tabelle zusammengefasst:
Bewertung hybrider Systeme
Vorteile | Nachteile |
---|---|
Flexibilität | Komplexität |
Kann sich wechselnden Anforderungen und unterschiedlichen Betriebsmodi anpassen. | Höhere Komplexität in der Steuerung und im Management. |
Kostensersparnis | Anfangsinvestition |
Geringere Automatisierungskosten im Vergleich zu vollautomatischen Systemen. | Höhere Anfangsinvestition als rein manuelle Systeme. |
Skalierbarkeit | Wartungsbedarf |
Einfacher zu erweitern oder zu modifizieren als vollautomatisierte Systeme. | Regelmäßige Wartung der automatisierten und manuellen Komponenten erforderlich. |
Effizienz und Genauigkeit | Abhängigkeit von menschlicher Arbeit |
Erhöht die Lagerhaltungseffizienz und Genauigkeit durch Automatisierung. | Weiterhin abhängig von qualifiziertem Personal für bestimmte Aufgaben. |
Beispiele für hybride Hochregallager - Hier sind einige Beispiele, wo man vorwiegend hybride Systeme findet.
Einzelhandelsdistributionzentren: Viele große Einzelhandelsketten nutzen hybride Systeme, um die Flexibilität zu haben, sowohl schnelle automatisierte Abwicklungen für gängige Produkte als auch manuelle Prozesse für spezielle, weniger häufige Artikel zu nutzen.
E-Commerce-Fulfillment-Zentren: Hybride Systeme ermöglichen es, den Großteil der Bestellungen automatisiert zu bearbeiten, während spezielle Kundenanforderungen oder Rücksendungen manuell behandelt werden können.
Lebensmittelindustrie: In der Lebensmittellogistik, wo oft mit verschiedenen Temperaturen und Produktspezifikationen gearbeitet wird, bieten hybride Systeme eine Kombination aus effizienter automatisierter Lagerung und der Notwendigkeit, manuell auf spezifische Bedingungen einzugehen.
Aufbau und Funktion eines Hochregallagers
Das Hochregallager repräsentiert eine fortschrittliche und effiziente Form der Lagerung, die insbesondere in dicht besiedelten Gebieten, wo jeder Quadratmeter wertvoll ist, von großem Nutzen ist. Diese Lager nutzen die verfügbare Höhe optimal aus und ermöglichen die Lagerung von Gütern auf relativ kleiner Grundfläche. Hochregallager können zwischen 12 und 50 Meter hoch sein und sind in der Lage, von einigen tausend bis zu mehreren hunderttausend Palettenstellplätzen zu fassen. Sie sind typischerweise aus Stahl konstruiert, aber es gibt auch Beispiele für Holzkonstruktionen, wie die sechs Holz-Hochregallager in Europa, von denen das höchste eine Höhe von 30 Metern erreicht.
In diesen Lagern bewegen sich Regalbediengeräte (RBG) oder Shuttle-Fahrzeuge in den Gassen zwischen den Regalen, um Waren ein- und auszulagern. Diese Geräte können entweder vollautomatisch gesteuert oder manuell bedient werden, abhängig davon, ob in der Vorzone oder direkt im Regal kommissioniert wird. Bei vollautomatischen Systemen sind die Bereiche aus Sicherheitsgründen oft durch Zäune und Lichtschranken abgesichert.
Die Konstruktion eines Hochregallagers kann auch in Silobauweise erfolgen, bei der das Regal selbst die tragende Konstruktion für Dach und Fassade bildet. Diese Bauweise spart weitere Fläche und Material und ist ein Beispiel für die effiziente Nutzung von Ressourcen.
Die automatische Steuerung dieser Lager wird durch ein Lagerverwaltungssystem unterstützt, das die Zuweisung von Regalplätzen übernimmt und sicherstellt, dass jeder Artikel im optimal passenden Fach gelagert wird. In der Vorzone des Lagers erfolgt die Anlieferung und Vorbereitung der Waren für die Einlagerung. Hier finden auch die Kommissionierung und die Vorbereitung der Waren für den Versand statt. Identifikationssysteme wie Barcodes oder Smart Labels helfen dabei, die Waren im System zu erfassen und ihren Weg durch das Lager zu verfolgen.
Zu den Komponenten der Fördertechnik in solchen Lagern gehören Kettenförderer, Rollenbahnen, Hubtische, Drehtische und fahrerlose Transportfahrzeuge, die alle dazu beitragen, die Effizienz und Geschwindigkeit der Lagerprozesse zu erhöhen. Dies macht das Hochregallager zu einem kritischen Element moderner Logistiksysteme, das auf die Anforderungen verschiedenster Branchen zugeschnitten ist.
Man unterscheidet z.B. folgende Bauweisen von Hochregallagern:
Standardbauweise: Die meisten Hochregallager sind so konstruiert, dass zwischen zwei Regalreihen eine Gasse für Förder- und Bediengeräte verläuft. Die Regalreihen sind in der Regel „Rücken an Rücken“ angeordnet, was eine einfachtiefe Lagerung ermöglicht. Diese Anordnung erlaubt es, jeden Lagerplatz direkt anzufahren und optimiert somit die Zugriffszeiten.
Silobauweise: Eine spezielle Form des Hochregallagers ist die Silobauweise, bei der die Regale selbst als tragende Konstruktion für Seitenwände und Dach dienen. Diese Bauweise erfordert keine zusätzliche Lagerhalle, was insbesondere bei begrenzten Platzverhältnissen oder hohen Baukosten Vorteile bietet.
Bei den Belastungsarten in Hochregallagern werden unterschieden:
Feldlast: Unter Feldlast versteht man die gesamte Tragkraft der Regalfächer zwischen zwei Regalständern. Sie wird berechnet, indem die Belastungen aller Regalfächer eines Feldes addiert werden, ohne das Eigengewicht des Regals zu berücksichtigen.
Fachlast: Die Fachlast bezieht sich auf die Tragkraft eines einzelnen Regalfachs. Die Summe aller Fachlasten innerhalb eines Feldes ergibt die Feldlast. Dies ist wichtig für die korrekte Dimensionierung der Regalständer und die Sicherheit des Lagerbetriebs.
Regalarten in Hochregallagern - Die Arten der Regale unterscheiden sich wie folgt:
Palettenregale: Entwickelt für die Lagerung von palettierten Gütern und weit verbreitet in der Industrie.
Kragarmregale: Ideal für die Lagerung von langen Gütern wie Rohren oder Brettern.
Fachbodenregale: Eignen sich besonders für manuell zu kommissionierende Kleinteile.
Schwerlastregale: Für besonders schwere Lasten ausgelegt.
Umlaufregale: Automatisierte Systeme, die die Güter zum Bediener transportieren.
Verfahrbare Regalsysteme: Mobile Regale, die den Platz optimal ausnutzen, indem sie nur bei Bedarf die notwendigen Gassen öffnen.
Kraftbetriebene verschiebbare Paletten- und Fachbodenregale: Eine Kombination aus Mobilität und Kraftantrieb für schwerere Lasten.
Aktenregale: Speziell für die Lagerung von Dokumenten in Büroumgebungen.
Langgurtregale, Einfahrregale und Durchfahrregale: Verschiedene Varianten für spezifische Lageranforderungen, etwa bei großen Mengen gleichartiger Güter.
Hochregale: Besonders hohe Regale, die speziell für Hochregallager konzipiert sind.
Regalsysteme in Kühlhäusern: Angepasst an die Bedingungen gekühlter Umgebungen.
Technologieeinsatz (z. B. ASRS)
Ein automatisiertes Hochregallager verwendet eine Hierarchie von Kontroll- und Steuerungsebenen, um den effizienten Betrieb und die Automatisierung von Lagerprozessen zu ermöglichen. Siehe folgendes Bild. Hier sind die Definitionen und Beispiele für die verschiedenen Ebenen:
Steuerungsebene (Managementebene):
Funktion: Koordination und Überwachung der Gesamtoperationen im Lager. Sie ist zuständig für die Verarbeitung von Daten, die Entscheidungsfindung und die Kommunikation mit den übergeordneten Unternehmenssystemen.
Beispielkomponenten - Lagerverwaltungssystem (LVS): Steuert die logistischen Abläufe, wie z.B. die Lagerplatzverwaltung und die Bestandskontrolle.
Materialflussrechner (MFR): Optimiert den Materialfluss durch das Lager und steuert automatisierte Transportmittel wie Förderbänder und Sortiersysteme.
Feldebene (Kontrollebene):
Funktion: Steuerung der direkten Interaktion mit den physischen Komponenten des Lagers. Diese Ebene enthält Geräte, die Daten sammeln und Aktionen basierend auf Befehlen von der Steuerungsebene ausführen.
Beispielkomponenten - Programmierbare Logikcontroller (PLC): Steuern Maschinen und Prozesse im Lager.
SCADA-Systeme (Supervisory Control and Data Acquisition): Überwachen und steuern industrielle Prozesse auf Feldebene.
Aktionsebene (Ausführungsebene):
Funktion: Physische Ausführung von Aufgaben wie das Bewegen, Heben und Sortieren von Lagergütern.
Beispielkomponenten - Sensoren: Erfassen Zustände und Daten, z.B. Barcodeleser, Lichtschranken und Drucksensoren.
Aktoren: Führen mechanische Bewegungen aus, z.B. Motoren, pneumatische Zylinder und Servos.
Elektromechanische Systeme: Spezialisierte Geräte wie Roboterarme oder automatische Fördersysteme.
Einsatz moderner Technologien im Hochregallager
Der technologische Fortschritt hat die Organisation und Verwaltung von Hochregallagern maßgeblich revolutioniert. Der Einsatz moderner Systeme wie Lagerverwaltungssysteme (LVS), Radiofrequenz-Identifikation (RFID) und automatisierter Lager- und Retrievalsysteme (Automated Storage and Retrieval-Systems, ASRS) hat sowohl die Effizienz als auch die Genauigkeit der Lagerprozesse erheblich gesteigert. Diese Technologien ermöglichen eine optimale Nutzung der verfügbaren Ressourcen und minimieren gleichzeitig menschliche Fehler.
Automatisierte Lager- und Retrievalsysteme (ASRS)
Automatisierte Lager- und Retrievalsysteme (ASRS) bilden häufig das Kernstück moderner Hochregallager. Sie nutzen fortschrittliche Robotik und präzise Steuerungssysteme, um Waren effizient ein- und auszulagern. Typische Komponenten eines ASRS sind:
Regalbediengeräte (RBG)
Regalbediengeräte sind vertikale Kräne, die entlang von Schienen zwischen den Regalreihen fahren. Sie übernehmen die Aufgabe, Waren auf unterschiedlichen Höhen und Tiefen innerhalb der Regale zu platzieren oder abzuholen. Durch ihre präzise Steuerung können sie schwere Lasten sicher bewegen und auch in hochdichten Lagersystemen mit schmalen Gängen operieren. Ein Beispiel für den Einsatz ist die Automobilindustrie, in der RBGs Ersatzteile mit hoher Genauigkeit bereitstellen.
Regalbediengeräte sind zentrale Elemente in modernen Lagersystemen und zeichnen sich durch ihre Anpassungsfähigkeit an unterschiedliche Lageranforderungen aus. Man unterscheidet z.B. Einmast- und Zweimast-Regalbediengeräte, die jeweils für spezifische Lagerbedingungen konzipiert sind.
Hier sind einige Beispiele:
Einmast-Regalbediengeräte sind ideal für Lager mit hohem Warenumschlag und können in Lagerhöhen von bis zu 45 Metern eingesetzt werden. Diese Geräte funktionieren effizient in Regalsystemen einfacher oder doppelter Tiefe und sind kompatibel mit dem Pallet Shuttle-System, das eine automatisierte Ein- und Auslagerung von Paletten ermöglicht.
Zweimast-Regalbediengeräte bieten eine höhere Tragfähigkeit und eignen sich ebenfalls für Lager mit hohem Umschlag. Der wesentliche Unterschied zum Einmast-System liegt in der Fähigkeit, Lasten in doppelter Tiefe aufzunehmen und zwei Lastaufnahmemittel gleichzeitig zu handhaben.
Automatisierte Regalbediengeräte mit Schwenkschubgabel erweitern die Funktionalität durch ihre Fähigkeit, die Lasten zu drehen und seitlich zu verschieben, was eine flexible Handhabung in komplexen Lagersituationen ermöglicht.
Komponenten der Regalbediengeräte - Die Komponenten der Regalbediengeräte umfassen
Fußteil: Eine kastenförmige Struktur mit Antriebs- und Laufrad ermöglicht die Bewegung des Gerätes entlang des Lagers.
Masten: Gefertigt aus hochfestem Stahl, sind sie die tragende Struktur, an der die Hubplattform entlangfährt.
Hubplattform: Diese Plattform führt die vertikale Bewegung aus und handhabt die Ein- und Auslagerung der Paletten.
Hubantrieb: Ein Wechselstrommotor bewegt die Hubplattform auf und ab.
Kopfteil: Sorgt für die Stabilität des Geräts und dämpft Lärm und Vibrationen bei hoher Bewegungsgeschwindigkeit.
Umsetzbrücke und Kurvenumsetzer: Beide ermöglichen das Verfahren des Regalbediengeräts von einem Gang zum anderen, wobei der Kurvenumsetzer eine schienenartige Lösung bietet.
Schaltschrank: Angebracht am Mast, versorgt dieser das Gerät mit Strom.
Ausstattung der Gänge: Diese umfasst Lauf- und Führungsschienen sowie Systeme für Sicherheit, Stromversorgung, Datenübertragung und Positionsbestimmung.
Regalbediengeräte sind entscheidende Lösung zur Automatisierung von Lagerprozessen, die auf die spezifischen Anforderungen und Gegebenheiten jedes Lagers zugeschnitten sind. Sie tragen wesentlich zur Optimierung des Warenumschlags und zur Erhöhung der Lagerkapazität bei.
Förderbänder und Transportbahnen
Förderbänder verbinden verschiedene Bereiche eines Hochregallagers, wie Ladezonen, Bearbeitungsstationen und Lagerplätze. Sie gewährleisten den schnellen und sicheren Transport von Gütern und minimieren dabei die Durchlaufzeiten. In der Lebensmittelindustrie kommen Förderbänder häufig zum Einsatz, um Waren unter strengen hygienischen Bedingungen von der Lagerung zur Verpackung zu transportieren
Shuttle-Systeme
Shuttle-Systeme sind autonome Fahrzeuge, die in komplexeren Lagereinrichtungen verwendet werden. Diese Systeme bewegen sich unabhängig voneinander und können auf mehreren Ebenen und in unterschiedlichen Gängen arbeiten.
Radiofrequenz-Identifikation (RFID)
RFID-Technologie spielt eine wichtige Rolle in der modernen Lagerlogistik. Durch RFID-Chips können Waren automatisch identifiziert und verfolgt werden, ohne dass ein direkter Sichtkontakt erforderlich ist. Diese Technologie ermöglicht eine Echtzeitüberwachung des Warenflusses und hilft, Lagerbestände effizient zu verwalten.
Ein Beispiel ist der Einsatz von RFID in Mode- und Textillagern, wo Produkte häufig in großen Mengen und unterschiedlichen Variationen gelagert werden. RFID erleichtert hier nicht nur die Inventur, sondern auch die schnelle Bereitstellung von Waren für den Versand.
Vorteile moderner Technologien im Hochregallager - Der Einsatz moderner Technologien führt zu zahlreichen Vorteilen:
Effizienzsteigerung: Automatisierte Systeme wie ASRS und LVS minimieren den manuellen Aufwand und erhöhen die Durchlaufgeschwindigkeit.
Genauigkeit: Fehler bei der Ein- und Auslagerung werden durch die präzise Steuerung der Systeme nahezu eliminiert.
Transparenz: Technologien wie RFID ermöglichen eine vollständige Nachverfolgbarkeit von Warenbeständen.
Platzoptimierung: Dynamische Lagerhaltung und der Einsatz von Shuttle-Systemen maximieren die Nutzung des verfügbaren Raums.
Lagerverwaltungssysteme (LVS)
Das LVS ist eine Softwareplattform, die die Bewegungen und den Status jeder Ware im Lager steuert und überwacht.
Trotz der offensichtlichen Vorteile sind moderne Technologien mit hohen Implementierungskosten verbunden. Die Anschaffung, Installation und Integration der Systeme erfordern erhebliche Investitionen. Außerdem ist die kontinuierliche Wartung der Hardware und Software entscheidend, um eine langfristige Leistungsfähigkeit zu gewährleisten. Eine weitere Herausforderung liegt in der Abhängigkeit von IT-Systemen, die im Falle von Störungen den gesamten Lagerbetrieb beeinträchtigen können.
Moderne Technologien wie ASRS, LVS und RFID haben die Prozesse in Hochregallagern grundlegend verändert. Sie ermöglichen eine hohe Effizienz, Genauigkeit und Transparenz, erfordern jedoch auch hohe Investitionen und regelmäßige Instandhaltung. Unternehmen, die auf solche Technologien setzen, profitieren langfristig von optimierten Lagerprozessen und einer gesteigerten Wettbewerbsfähigkeit.
Es integriert sich nahtlos in das ASRS und andere Lageroperationen, um Folgendes zu gewährleisten:
Bestandsoptimierung: Automatisierte Berichte und Echtzeit-Updates zum Lagerbestand helfen, Überbestände zu reduzieren und die Lagerkapazität optimal zu nutzen.
Auftragsabwicklung: Das System automatisiert die Kommissionierungsprozesse, optimiert die Routen und Sequenzen für die Entnahme und verbessert die Genauigkeit der Auftragszusammenstellung.
Datenanalyse und Reporting: Fortgeschrittene Analysetools innerhalb des LVS bieten Einblicke in Trends, Leistungsmetriken und ermöglichen die fortlaufende Optimierung der Lageroperationen.
Ein Lagerverwaltungssystem koordiniert und optimiert die Lagerorganisation. Es steuert die Ein- und Auslagerungsprozesse, überwacht den Warenbestand und sorgt für eine nahtlose Integration aller Lagertechniken. Das LVS ist häufig mit einem ERP-System verbunden, das die betriebswirtschaftliche Ebene des Unternehmens abdeckt.
Besonders vorteilhaft ist der Einsatz eines LVS in Kombination mit der dynamischen Lagerhaltung. Diese Methode, bei der Waren auf beliebige freie Plätze eingelagert werden, erhöht die Flächeneffizienz. Gleichzeitig ermöglicht das LVS die schnelle und präzise Lokalisierung der Ware, unabhängig davon, wo sie eingelagert wurde. In der Pharmaindustrie, wo hohe Sicherheitsstandards gelten, unterstützt das LVS zusätzlich die lückenlose Rückverfolgbarkeit von Produkten.
Pick-to-Light- und Put-to-Light-Systeme
Diese Technologien unterstützen das manuelle Kommissionieren durch optische Signale, die den Mitarbeitern zeigen, welche Artikel in welchen Mengen zu entnehmen oder abzulegen sind.
Sie verbessern die Geschwindigkeit und Genauigkeit beim manuellen Handling und verringern Fehler.
Einfache Integration: Diese Systeme lassen sich leicht in bestehende Lagerstrukturen einbauen und unterstützen eine effiziente Kommissionierung ohne umfangreiche Schulungen der Mitarbeiter.
Die ideale Nutzung dieser Technologien in einem Hochregallager umfasst: Maximierung des Raums: Durch die vertikale und tiefe Lagerung, ermöglicht durch hohe und tiefreichende Regalsysteme, wird die verfügbare Lagerfläche optimal genutzt.
Erhöhung der Lagerdichte: ASRS ermöglicht eine enge Lagerung von Gütern, da die Anlagen genau und ohne die Notwendigkeit breiter Gänge für Gabelstapler arbeiten können.
Reduzierung der Arbeitskosten und Steigerung der Sicherheit: Automatisierte Systeme reduzieren die Notwendigkeit menschlicher Eingriffe, was nicht nur Personalkosten spart, sondern auch das Risiko von Arbeitsunfällen.
Flexibilität und Skalierbarkeit: Automatisierte Systeme können an unterschiedliche Betriebsgrößen und saisonale Schwankungen angepasst werden, was sie ideal für Unternehmen macht, die in dynamischen Märkten tätig sind.
Maximale Raumausnutzung - welche Regale eignen sich als Hochregale?
Für die Auswahl von Regalsystemen in Hochregallagern sind die Tragkraft und die Beschaffenheit des Lagerguts entscheidende Faktoren. In einem Hochregallager, das mit über 1000 kg pro Palette beladen wird, summieren sich die Gewichte schnell auf tausende Tonnen pro Regalreihe. Dies stellt hohe Anforderungen an die Tragfähigkeit der unteren Etagen der Regalsysteme, was den Einsatz massiver Regaltypen erforderlich macht. Daher sind insbesondere Palettenregale oder Schwerlastregale für solche Belastungen geeignet. Auch Regalsysteme für Langgut lassen sich effektiv in die Höhe bauen, um den vertikalen Lagerraum optimal zu nutzen.

Beispiel Regalsystem für Langgut
Weniger geeignet für derartige Lasten sind hingegen Regalsysteme für Akten oder Kleinteile, da diese nicht für das Handling schwerer Lasten konzipiert sind. In der Planungsphase muss daher genau geprüft werden, welche Regaltypen den spezifischen Anforderungen eines Hochregallagers gerecht werden können.
Die chaotische Lagerhaltung
Die chaotische Lagerung, oft als dynamische Lagerhaltung bezeichnet, ist ein Logistikkonzept, das zur effizienten Nutzung der Lagerkapazität und zur Optimierung der Zugriffszeiten auf Artikel dient. Trotz der anfänglich negativen Konnotation des Begriffs „chaotisch“, beschreibt dieser eine flexible Platzierung von Waren im Lager, ohne feste Zuordnungen zu bestimmten Plätzen. Stattdessen kann jedes Lagergut an jedem verfügbaren Platz im Lager abgelegt werden, abhängig vom aktuellen freien Raum. Dieses System wird durch ein computergestütztes Lagerverwaltungssystem unterstützt, das genau verfolgt, wo jedes Teil gelagert ist.
Die Vorteile der chaotischen Lagerung zeigen sich besonders bei technischen Pannen. Durch die Verteilung der Waren über verschiedene Bereiche des Lagers und den Einsatz von Anlagenredundanzen bleibt der Zugriff auf die Waren gewährleistet, selbst wenn einzelne Geräte ausfallen. Diese Resilienz trägt dazu bei, dass Produktionsprozesse oft unbeeinträchtigt weiterlaufen können. Die hohe Verfügbarkeit und Zuverlässigkeit der Geräte, unterstützt durch regelmäßige Wartung und qualifiziertes Fachpersonal, verbessern zusätzlich die Effizienz und Stabilität des Lagerbetriebs.
Definition und Gestaltung
Ein Hochregallager wird definiert durch die beträchtliche Höhe der Regalsysteme, die ab einer Mindesthöhe von 12 Metern beginnt und aktuell bis zu einer Höhe von etwa 50 Metern reichen kann. Die technischen Herausforderungen und der damit verbundene Aufwand für die Stabilisierung der Regalstrukturen nehmen mit zunehmender Höhe zu. In Fällen besonders hoher Regalsysteme, die bis zur Decke reichen, wird häufig die Silobauweise angewendet, bei der die Regale selbst als tragende Elemente zur Stützung der Deckenstruktur dienen.
Der strukturelle Aufbau eines Hochregallagers folgt einem standardisierten Muster: Mehrere Regalreihen, typischerweise aus Stahl und seltener aus Holz, werden in regelmäßigen Abständen aufgestellt, um maximale Stabilität und Zugänglichkeit zu gewährleisten. Zwischen den Regalreihen befinden sich Gassen, die den Zugang zu den Waren mittels Förderzeugen oder speziellen Regalbediengeräten ermöglichen. Dieses einfache, aber effiziente Layout ermöglicht es, Lagerkapazitäten von bis zu mehreren hunderttausend Palettenplätzen zu realisieren
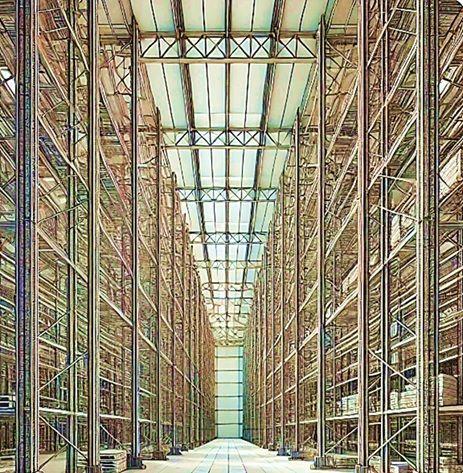
Silobauweise
Ein Hochregallager, bei dem die Regale als tragende Elemente die Deckenstruktur stützen bzw. tragen.
Die Dimensionierung der einzelnen Regalfächer variiert, um eine flexible Lagerung von Gütern unterschiedlicher Größen zu ermöglichen. Es wird jedoch empfohlen, die Lagerung auf einer standardisierten Basis, wie beispielsweise einer Europalette, durchzuführen. Diese Standardisierung ist besonders wichtig, da die Bediener der Fördergeräte die Regalfächer von unten nicht einsehen können, was die Handhabung der unterschiedlichen Lagerpositionen

Wege für Regalbediengeräte (schematisch)
Die Regalbediengeräte sind meist so konstruiert, dass sie sich nur zwischen jeweils zwei Reihen bewegen können. Das Verlassen der jeweiligen Gasse im Warenlager ist nicht vorgesehen. Meist wird der Fahrweg des Regalbediengerätes in alle Richtungen durch eine Führungsschiene begrenzt.
Wirtschaftliche Nachteile durch Platzverschwendung - Die Platzverschwendung ist nicht nur eine Frage der Raumnutzung, sondern hat auch direkte wirtschaftliche Konsequenzen:
Kapazitätsverlust: Unproduktiver Raum verringert die Lagerkapazität und erfordert gegebenenfalls zusätzliche Lagerflächen oder die Errichtung neuer Lager.
Kostensteigerung: Da Hochregallager eine hohe Investition pro Kubikmeter Lagerraum erfordern (oft 300–500 Euro pro m³), bedeutet ungenutzter Raum eine Verschwendung von Kapital.
Effizienzverluste: Die unnötige Belegung großer Regalfächer mit kleinen Artikeln verlängert auch die Fahrzeiten der Regalbediengeräte, da mehr Leerraum überwunden werden muss.
Vorteile der chaotischen Lagerhaltung
Vor- und Nachteile hoher Regalsysteme im Lager
Hohe Regalsysteme bieten eine Reihe von Vorteilen, insbesondere im Hinblick auf die effiziente Raumnutzung und die Automatisierung von Prozessen. Dennoch sind sie mit Einschränkungen und Herausforderungen verbunden, die insbesondere die Flexibilität und die Abhängigkeit von IT-Systemen betreffen. Um die Eignung eines solchen Systems zu bewerten, ist eine differenzierte Betrachtung der Vorteile und Nachteile erforderlich.
Effiziente Raumnutzung
Der größte Vorteil hoher Regalsysteme liegt in der optimalen Nutzung des vertikalen Raums. Während herkömmliche Lager oft lediglich in der Breite und Tiefe planen, können Hochregallager die verfügbare Raumhöhe bis knapp unter die Hallendecke ausnutzen. Insbesondere in städtischen Gebieten mit hohen Grundstückspreisen oder bei eingeschränkten Flächen ist dies ein entscheidender Vorteil.
Ein praktisches Beispiel sind Logistikzentren, die große Mengen an standardisierten Produkten lagern, wie beispielsweise die Automobilbranche, in der Ersatzteile gelagert werden. Hier ermöglicht die Silobauweise – bei der die Regale selbst als tragende Elemente für das Gebäude dienen – eine erhebliche Kostenersparnis, da keine separate Hallenstruktur erforderlich ist. Die Kostenreduktion durch die Integration von Bau- und Lagertechnik macht diese Bauweise besonders attraktiv für Großlager mit hoher Auslastung.
Flexibilität für wechselnde Bestände
Trotz der hohen Effizienz leidet die Flexibilität in einem Hochregallager. Die starren Strukturen der Regalsysteme lassen sich nur schwer an veränderte Lageranforderungen anpassen. Beispielsweise erfordert eine Umorganisation der Regale oft eine vollständige Sperrung einzelner Bereiche. Dies führt nicht nur zu Einschränkungen im laufenden Betrieb, sondern auch zu erhöhtem Aufwand und Kosten.
Ein Beispiel aus der Praxis sind saisonale Schwankungen im E-Commerce. Unternehmen, die wechselnde Produktpaletten verwalten, haben in starren Hochregalsystemen Schwierigkeiten, schnell auf veränderte Anforderungen zu reagieren. Selbst kleinere Änderungen, wie die Anpassung der Regalböden an andere Palettengrößen, können umfangreiche Umbauten erforderlich machen. Daher ist ein solches System vor allem für Unternehmen geeignet, die eine gleichbleibende Lagerstruktur und konstante Bestände verwalten.
Das Problem der Grenzraummaße
Der denkbare Widerspruch im Hochregallager zwischen der Auslegung auf maximale Lagergutmaße und der häufig auftretenden Lagerung von sehr kleinen Teilen ist ein zentrales Thema, das direkte Auswirkungen auf die Effizienz und Wirtschaftlichkeit hat. Dieses Problem lässt sich aus verschiedenen Perspektiven analysieren.
Hochregallager werden oft auf die Lagerung eines standardisierten maximalen Lagerguts ausgelegt. Typischerweise sind dies Paletten mit den Maßen 1.200 x 800 mm (Europalette) oder ähnliche standardisierte Ladungsträger. Auch die Höhe der Regalfächer ist in der Regel für eine maximale Beladung ausgelegt, beispielsweise bis zu 1.800 mm für Großvolumenartikel.
Wenn nun kleinere Lagergüter eingelagert werden – etwa Kleinladungsträger (KLTs) oder lose Teile –, führt dies zwangsläufig zu einer ineffizienten Raumnutzung. Oft bleibt ein erheblicher Anteil des Regalfachs ungenutzt, da der Lagerplatz nicht an kleinere Abmessungen angepasst werden kann.
Lösungsansätze zur Minderung des Problems
Das Problem der Grenzraummaße kann durch eine flexible Gestaltung der Lagerplätze und den Einsatz intelligenter Technologien entschärft werden:
Variable Regalfächer
Moderne Hochregallager ermöglichen oft eine Anpassung der Fachhöhen. Damit können die Regalfächer bei Bedarf für kleinere Lagergüter verkleinert werden.
Dies ist allerdings mit zusätzlichem Aufwand verbunden und bedarf sorgfältiger Planung.
Beispiel: Ein System mit höhenverstellbaren Regalböden könnte die Fächer von 1.800 mm auf 400 mm reduzieren, was die Lagerung von KLTs oder kleinteiligen Artikeln optimiert.
Kombination von Lagereinheiten: Statt kleine Teile direkt in die Regalfächer zu legen, können diese auf standardisierte Träger konsolidiert werden. Kleinladungsträger (KLTs) oder Sammelbehälter können mehrere Artikel bündeln und effizient in den Regalfächern gelagert werden.
Beispiel: 10 KLTs mit den Maßen 600 x 400 mm können auf einer Europalette gestapelt und als eine Lagereinheit behandelt werden.
Dynamische Lagerhaltung: Die dynamische (chaotische) Lagerhaltung sorgt dafür, dass freie Lagerplätze flexibel genutzt werden. Kombiniert mit der ABC-Strategie kann der ungenutzte Raum für größere Artikel reserviert werden, während kleinere Artikel an besser zugänglichen Standorten gelagert werden.
Grenzen und Herausforderungen - Trotz dieser Lösungen gibt es technische und wirtschaftliche Grenzen:
Statische Regalsysteme: In vielen bestehenden Hochregallagern sind die Fachhöhen fix und können nicht flexibel angepasst werden. Der Umbau solcher Systeme ist teuer und zeitaufwendig.
Maximale Tragfähigkeit: Kleinladungsträger oder Sammelbehälter erhöhen oft die Traglast eines Regalfachs, insbesondere bei gestapelten Einheiten. Die Traglastgrenzen (z. B. 500–1.000 kg pro Fach) müssen beachtet werden.
IT-Anforderungen: Eine effektive Verwaltung solcher Lösungen setzt leistungsfähige IT-Systeme voraus, die in der Lage sind, dynamische Lagerprozesse zu koordinieren und die Platznutzung zu optimieren.
Beispiele und Kenngrößen
Typische maximale Lagergüter: Europaletten (1.200 x 800 x 1.800 mm) oder Gitterboxen (1.240 x 835 x 970 mm).
Kleine Lagergüter: KLTs (600 x 400 x 200 mm) oder Kleinteile (z. B. Schrauben, die oft in Kartons von 300 x 200 x 150 mm gelagert werden).
Kapazitätsverlust: Ein Regalfach für eine Europalette mit 1.800 mm Höhe würde bei der Lagerung eines KLTs nur etwa 20–25 % des verfügbaren Volumens nutzen.
Lagerkosten: Wenn der Raum ineffizient genutzt wird, steigen die Kosten pro gelagerte Artikel erheblich. Bei einer ungenutzten Fläche von 50 % verdoppeln sich die pro Artikel anfallenden Lagerkosten.
Der Widerspruch zwischen der Auslegung auf maximale Lagergüter und der Lagerung kleiner Teile in Hochregallagern ist eine zentrale Herausforderung. Effiziente Raumnutzung und Wirtschaftlichkeit können durch flexible Regalsysteme, konsolidierte Lagereinheiten und dynamische Lagerhaltungsstrategien verbessert werden. Dennoch bleiben technische und wirtschaftliche Grenzen bestehen, die bei der Planung und Optimierung von Hochregallagern berücksichtigt werden müssen. Ein gezielter Einsatz moderner Technologien und eine flexible Gestaltung können jedoch dazu beitragen, diesen Widerspruch weitgehend zu entschärfen.
Abhängigkeit von IT-Systemen
Die Steuerung und Verwaltung eines Hochregallagers sind stark von IT-Systemen abhängig. Diese Systeme umfassen meist eine komplexe Struktur aus einem ERP-System, einem Lagerverwaltungssystem (LVS) und einem Materialflussrechner. Während das ERP-System als übergeordnetes System die Geschäftsprozesse koordiniert, optimiert das LVS die Lagerorganisation und der Materialflussrechner übernimmt die Steuerung der Fördertechnik und Regalbediengeräte.
Ein zentraler Vorteil dieser IT-Abhängigkeit ist die Möglichkeit, Lagerflächen effizient zu organisieren. Zum Beispiel wird häufig die dynamische Lagerhaltung eingesetzt, bei der Waren nicht an festen Plätzen, sondern auf beliebigen freien Lagerplätzen eingelagert werden. Dieses „chaotische“ Prinzip kann durch zusätzliche Regeln ergänzt werden, um die Verfügbarkeit der Ware zu maximieren. So kann festgelegt werden, dass Container eines Materials auf mehrere Regalbediengeräte verteilt werden. Sollte ein Gerät ausfallen, bleibt die Ware dennoch zugänglich.
Zusätzlich wird in Hochregallagern häufig die ABC-Strategie angewendet. Artikel mit hoher Umschlaghäufigkeit werden im A-Bereich in der Nähe der Ein- und Auslagerplätze gelagert, wodurch die Wege und damit die Einlagerungszeiten minimiert werden. Artikel mittlerer Häufigkeit befinden sich im B-Bereich, während der C-Bereich für selten benötigte Waren reserviert ist. Dieses System ermöglicht eine hohe Effizienz bei der Lagerorganisation, ist jedoch abhängig von einer zuverlässigen und leistungsfähigen IT-Infrastruktur.
Implementierungskosten
Die Implementierung eines Hochregallagers erfordert erhebliche Investitionen. Neben den Kosten für die Bau- und Lagertechnik sind auch die Ausgaben für die IT-Infrastruktur und deren Anpassung an die spezifischen Anforderungen des Unternehmens zu berücksichtigen (Schnittstellenmanagement). Besonders bei der Integration von ERP- und Lagerverwaltungssystemen entstehen zusätzliche Kosten für die Softwareanpassung und die Schulung des Personals.
Ein Beispiel für die hohen Implementierungskosten ist der Aufbau eines automatisierten Lagers in der Lebensmittelindustrie, wo strenge Anforderungen an Temperatur und Hygiene gestellt werden. Hier müssen neben den Regalsystemen auch spezielle Kühltechniken und Sensoren integriert werden, die wiederum mit der IT verknüpft sind. Obwohl die Kosten hoch sind, können sich solche Investitionen langfristig auszahlen, da sie die Lagerprozesse erheblich beschleunigen und die Fehlerquote reduzieren.
Fazit
Hohe Regalsysteme bieten vor allem in Bereichen mit großem Lagerbedarf und gleichbleibenden Beständen eine effiziente und kostensparende Lösung. Sie sind jedoch mit Einschränkungen in der Flexibilität und einer hohen Abhängigkeit von IT-Systemen verbunden. Unternehmen sollten daher sorgfältig prüfen, ob sich die Investition in ein Hochregallager langfristig lohnt und mit ihren Anforderungen vereinbar ist.