Strategische Instandhaltung für zuverlässige Hochregallager
Facility Management: Lagerimmobilien » Grundlagen » Instandhaltung
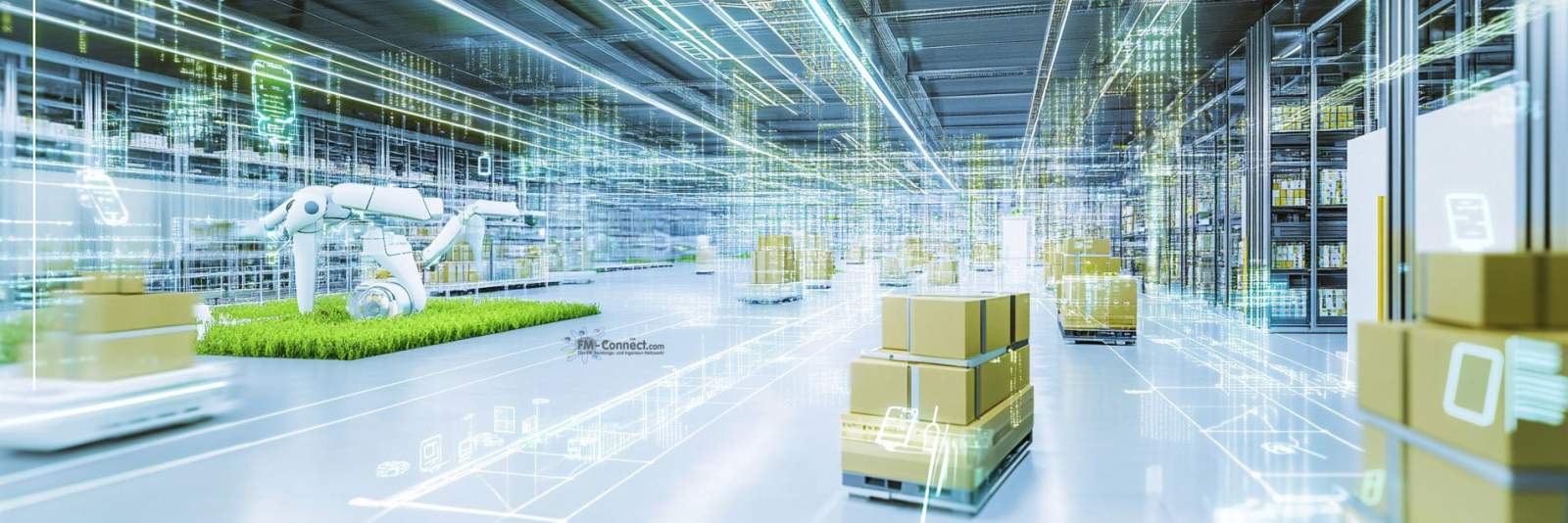
Instandhaltung von Hochregallagern strategisch absichern
Die Instandhaltung von Hochregallagern stellt eine komplexe und herausfordernde Aufgabe dar, die hohe Anforderungen an die Präzision, Schnelligkeit und Sicherheit der durchgeführten Arbeiten stellt. Wie aus den Erfahrungen von Fachleuten hervorgeht, ist eine umfassende Strategie erforderlich, um die Funktionsfähigkeit dieser Lager aufrechtzuerhalten und größere Betriebsstörungen zu vermeiden.
Fehlerbehebung im Facility Management
- Fehlerbehebung
- Zuständigkeiten
- Allgemeine
- Überlastungskontrolle
- Führungssystemen
- Schadensbewertung
- Grenzwerte
- Zeitbasierte
Schnelle Fehlerbehebung und erforderliche Ressourcen
Erfahrenes Personal: Die Bedeutung von gut ausgebildeten und erfahrenen Technikern kann nicht genug betont werden. Ihre Fähigkeit, Fehler schnell zu diagnostizieren und zu beheben, ist entscheidend für die Minimierung von Ausfallzeiten im Lagerbetrieb.
Ersatzteilvorrat: Ein angemessen geführter Vorrat an Ersatzteilen ist ebenfalls kritisch. Die Verfügbarkeit von sofort einsetzbaren Komponenten beschleunigt Reparaturen und reduziert die Zeit, in der Anlagen nicht genutzt werden können.
Herausforderungen und Lösungen in der Höhe
Arbeiten in großer Höhe: Alle Arbeiten in der Höhe sind besonders anspruchsvoll und zeitintensiv. Der Aufbau von Gerüsten oder der Einsatz spezieller Sicherheitsvorkehrungen wie Sicherheitsgurte und -netze sind erforderlich, um die Sicherheit des Personals zu gewährleisten.
Materialtransport: Die Verwendung von Lastaufnahmemitteln erleichtert den Transport von Materialien zu den Reparaturstellen. In manchen Fällen, besonders bei größeren Reparaturen oder Austauschaktionen, kann es sogar notwendig sein, Teile der Lagerstruktur temporär zu öffnen oder zu entfernen.
Präventive Maßnahmen und Tests
Regelmäßige Überprüfungen: Wichtige Sicherheitsüberprüfungen, wie die jährlich wiederkehrenden Prüfungen der Fangvorrichtungen und Geschwindigkeitsbegrenzer, sind unerlässlich. Diese Tests stellen sicher, dass im Falle eines Fehlers die Sicherheitssysteme wie Fangbremsen korrekt funktionieren und somit größere Katastrophen verhindern.
Externe Sichtweisen: Der Einsatz externer Sachverständiger für bestimmte Prüfungen kann dabei helfen, eine Betriebsblindheit zu vermeiden. Die andere Perspektive und spezialisierte Expertise von Prüfern des TÜV oder anderen Organisationen tragen zur Qualitätssicherung bei.
Flexibilität und Kommunikation
Notfallpläne: Es ist wichtig, flexible Notfallpläne (Plan B und C) zu haben, um auf Störungen im Betrieb adäquat reagieren zu können. Diese Pläne gewährleisten, dass das Lager auch bei unvorhergesehenen Problemen funktionsfähig bleibt.
Kommunikation: Eine gute interne Kommunikation ist essenziell, um sicherzustellen, dass das gesamte Team jederzeit informiert und koordiniert handeln kann. Dies unterstützt die Aufrechterhaltung der Lieferfähigkeit und die schnelle Behebung von Problemen.
Effiziente Wartung durch Planung und Fachkompetenz
Insgesamt erfordert die Instandhaltung von Hochregallagern eine sorgfältige Planung, hochqualifiziertes Personal und eine ausgezeichnete Organisationsstruktur, um effizient und sicher zu operieren.
Wartungsmanagement und Aufgabenverteilung im Facility Management
In vielen Unternehmen ist es gängige Praxis, dass ein Teil der Wartungsarbeiten intern durchgeführt wird, da die Mitarbeiter direkt für das Beheben von Störungen an Förderanlagen zuständig sind. Oftmals erlauben es die zeitlichen Kapazitäten jedoch nicht, sämtliche Wartungsarbeiten selbst durchzuführen, weshalb Wartungsdienstleistungen zusätzlich z.B. beim Hersteller erworben werden. Dabei ist es nicht unüblich, dass ein ständiger Mitarbeiter des Herstellers vor Ort ist, speziell für die Wartung von automatisierten Regalbediengeräten.
Dieser externe Mitarbeiter ist jedoch nicht in der Lage, alle Aufgaben eigenständig zu bewältigen. Bestimmte Tätigkeiten, wie Arbeiten in großer Höhe, erfordern aus Sicherheitsgründen eine zweite Person. Zudem werden für spezialisierte Aufgaben wie die Wartung von Sprinkleranlagen und Dachluken externe Firmen hinzugezogen. Auch für spezifische Prüfungen wie die Elektromessung, die Einhaltung von Unfallverhütungsvorschriften und die gesetzlich vorgeschriebene Regalprüfung, die alle fünf Jahre erforderlich ist, muss auf externes Personal zurückgegriffen werden.
Es ist also erforderlich, wie bereits an anderer Stelle bezüglich des Instandhaltungskonzeptes ausgeführt, notwendig, den beteiligten Personen klare und unmissverständliche Aufgaben zuzuweisen (Stellenbeschreibungen). Dabei sind auch die Schnittstellen zwischen eigenem und Fremdpersonal zu berücksichtigen.
Präventive Instandhaltung (Inspektion)
In vielen Unternehmen ist es gängige Praxis, dass ein Teil der Wartungsarbeiten intern durchgeführt wird, da die Mitarbeiter direkt für das Beheben von Störungen an Förderanlagen zuständig sind. Oftmals erlauben es die zeitlichen Kapazitäten jedoch nicht, sämtliche Wartungsarbeiten selbst durchzuführen, weshalb Wartungsdienstleistungen zusätzlich z.B. beim Hersteller erworben werden. Dabei ist es nicht unüblich, dass ein ständiger Mitarbeiter des Herstellers vor Ort ist, speziell für die Wartung von automatisierten Regalbediengeräten.
Dieser externe Mitarbeiter ist jedoch nicht in der Lage, alle Aufgaben eigenständig zu bewältigen. Bestimmte Tätigkeiten, wie Arbeiten in großer Höhe, erfordern aus Sicherheitsgründen eine zweite Person. Zudem werden für spezialisierte Aufgaben wie die Wartung von Sprinkleranlagen und Dachluken externe Firmen hinzugezogen. Auch für spezifische Prüfungen wie die Elektromessung, die Einhaltung von Unfallverhütungsvorschriften und die gesetzlich vorgeschriebene Regalprüfung, die alle fünf Jahre erforderlich ist, muss auf externes Personal zurückgegriffen werden.
Es ist also erforderlich, wie bereits an anderer Stelle bezüglich des Instandhaltungskonzeptes ausgeführt, notwendig, den beteiligten Personen klare und unmissverständliche Aufgaben zuzuweisen (Stellenbeschreibungen). Dabei sind auch die Schnittstellen zwischen eigenem und Fremdpersonal zu berücksichtigen.
Zustandsüberwachung
Der effiziente Betrieb und die Instandhaltung von Lagersystemen erfordern eine rigorose Zustandsüberwachung, die als zentrale Maßnahme der präventiven Instandhaltung angesehen wird. Dies wird durch verschiedene gesetzliche Regelungen und Normen untermauert, die in Deutschland und Europa für die Sicherheit und Funktionalität von Lageranlagen sorgen.
Präventive Instandhaltung durch Zustandsüberwachung
Die Zustandsüberwachung in Lagersystemen umfasst regelmäßige Inspektionen und Wartungen, um Schäden frühzeitig zu erkennen und zu beheben, bevor sie zu größeren Sicherheitsrisiken oder Betriebsstörungen führen. Die Betriebssicherheitsverordnung legt fest, dass Arbeitsmittel, die schädlichen Einflüssen ausgesetzt sind und potenziell gefährlich werden könnten, regelmäßig von einer befähigten Person geprüft werden müssen.
Bedeutung der Prüffristen
Die DIN EN 15635 legt eine Mindestprüffrist von einem Jahr für die Inspektion von Lagereinrichtungen vor, was die Bedeutung der präventiven Instandhaltung unterstreicht. Diese Frist dient dazu, die Sicherheit und Funktionalität der Anlagen kontinuierlich zu überprüfen und zu erhalten.
Die Zustandsüberwachung ist ein unerlässlicher Bestandteil der präventiven Instandhaltung von Lagersystemen. Sie wird durch eine Kombination aus gesetzlichen Anforderungen und Normen unterstützt, die sicherstellen, dass Lageranlagen sicher und effizient betrieben werden können. Diese regelmäßigen Überprüfungen sind entscheidend, um die Langlebigkeit der Anlagen zu gewährleisten und um einen sicheren Arbeitsplatz für alle Beteiligten zu garantieren.
Überwachungsstufen
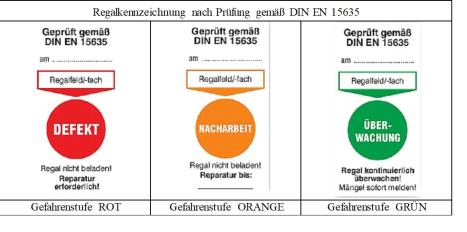
Gefahrenstufen (Kennzeichnung und Klassifizierung gem. DIN EN 15635)
Regalprüfung nach DIN EN 15635 zeigt drei Zustände: defekt, nacharbeitspflichtig oder überwacht – für verlässliche Sicherheit.
Bei der Überwachung und Instandhaltung von Regalsystemen wird ein gestuftes Warnsystem angewendet, das durch unterschiedliche Gefahrenstufen gekennzeichnet ist, um auf verschiedene Arten von Schäden und deren Schweregrad zu reagieren. Diese Stufen - Grün, Orange und Rot - signalisieren den aktuellen Zustand der Regalkomponenten und legen fest, welche Maßnahmen ergriffen werden müssen.
Gefahrenstufen (Kennzeichnung und Klassifizierung gem. DIN EN 15635)
Grüne Gefahrenstufe: Die grüne Gefahrenstufe stellt die Basisstufe dar, bei der die Grenzwerte, wie in der Dokumentation festgelegt, nicht überschritten wurden. Bauteile in dieser Kategorie werden als sicher und voll funktionsfähig angesehen, ohne dass eine sofortige Reparatur notwendig ist. Diese Komponenten erfordern keine Maßnahmen außer einer regulären Überwachung bis zur nächsten geplanten Inspektion. Obwohl keine sofortige Gefahr besteht, sollten solche Bauteile für eine spezielle Überprüfung bei zukünftigen Inspektionen gekennzeichnet werden, um sicherzustellen, dass keine Verschlechterung des Zustands eintritt. Eine solche systematische Überwachung gewährleistet, dass frühe Anzeichen von Abnutzung oder Schäden rechtzeitig erkannt und adressiert werden können, bevor sie schwerwiegende Probleme verursachen.
Orange Gefahrenstufe: Im Gegensatz dazu weist die orange Gefahrenstufe auf eine ernsthafte Beschädigung hin, die umgehendes Handeln erfordert, jedoch nicht so kritisch ist, dass eine sofortige Entladung des Regals notwendig wäre. In dieser Stufe überschreiten die Schäden die festgelegten Grenzwerte deutlich, erfordern aber einen Austausch des beschädigten Teils, bevor das Regal wieder beladen werden darf. Zur Sicherstellung, dass diese Regalbereiche nicht weiter benutzt werden, sollten klare Kennzeichnungen, wie datierte Aufkleber, angebracht werden, die das Verbot der Nutzung bis zur Durchführung der Reparatur signalisieren. Sollten diese Schäden nicht innerhalb eines angemessenen Zeitraums – typischerweise vier Wochen – repariert werden, müssen die betroffenen Bereiche in die rote Gefahrenstufe hochgestuft werden.
Rote Gefahrenstufe: Die rote Gefahrenstufe indiziert eine sehr schwere Beschädigung, bei der die Grenzwerte um das Doppelte oder mehr überschritten wurden. In solchen Fällen muss das betroffene Regalsegment sofort entladen und für den Gebrauch gesperrt werden, bis eine angemessene Reparatur durchgeführt worden ist. Dies erfordert in der Regel den Austausch des beschädigten Bauteils. Es müssen effektive Maßnahmen zur Absperrung dieser Zonen getroffen werden, um eine weitere Nutzung zu verhindern, wie das Einrichten physischer Barrieren oder das Anbringen von Warnschildern.
Die Etablierung und Einhaltung dieser Überwachungsstufen sind entscheidend für die Aufrechterhaltung der Sicherheit und Funktionalität von Lageranlagen. Durch frühzeitige Identifizierung und Adressierung potenzieller Risiken tragen diese Maßnahmen wesentlich zur Vermeidung von Unfällen und zur Verlängerung der Lebensdauer der Lagerinfrastruktur bei.
Allgemeine Inspektionen
Regelmäßigkeit und Systematik: Inspektionen aller Lagereinrichtungen sind systematisch und regelmäßig durchzuführen, vorrangig vom Boden aus, da hier die meisten Beschädigungen auftreten. Höhergelegene Inspektionen erfordern sichere Zugangsweisen, wobei eine einfache Besteigung der Regale nicht zulässig ist.
Bestimmung der Inspektionsfrequenz: Die Frequenz und der Umfang der Inspektionen werden durch mehrere Faktoren bestimmt, darunter die Betriebsbedingungen des Lagers, die Lagergröße, die eingesetzten Einrichtungen und das Personal. Alle diese Faktoren tragen zur Wahrscheinlichkeit einer Beschädigung der Konstruktion bei. Die spezifischen Inspektionspläne sind vom Sicherheitsbeauftragten festzulegen.
Spezifische Inspektionsverfahren
Sofortige Meldung: Entdeckt eine Person ein Sicherheitsproblem oder einen Schaden, muss der Sicherheitsbeauftragte unverzüglich informiert werden.
Regelmäßige Sichtkontrollen: Wöchentlich oder nach einer Risikoanalyse sind Sichtkontrollen durchzuführen. Hierbei ist ein formaler, schriftlicher Bericht zu erstellen.
Experteninspektionen
Fachkundige Personen führen jährlich Inspektionen durch, die mindestens 20% der Anlage umfassen, mit einem rollierenden Plan, sodass die gesamte Anlage alle 60 Monate inspiziert wird. Ein schriftlicher Bericht über Beobachtungen und jegliche erforderlichen Maßnahmen ist dem Sicherheitsbeauftragten zu übergeben.
Schadenuntersuchung und -kontrolle
Ursachenanalyse: Zu untersuchen sind potentielle Ursachen jedes Schadens, um das Problem und eine Wiederholung der Schäden zu reduzieren oder zu beseitigen.
Ursachenanalyse bei jedem Schaden
Bei jeglichem Schaden müssen die potentiellen Ursachen des Problems untersucht werden, damit das Problem und eine Wiederholung der Schäden reduziert oder beseitigt werden kann. Geeignete Maßnahmen sind entsprechend vorzunehmen.
Über die Gründe für das Auftreten der Schäden muss eine Schlussfolgerung gezogen werden. Hier sind einige idealtypische Ergebnisse (nicht umfassend):
falsche Anlagenbedienung
falsche Staplerbedienung
Qualität der Gabelstaplerfahrerschulung bzw. Fortbildung
Änderung des ursprünglichen Fördermittels
Zustandsmängel am Fördermittel
Änderung der Palette nötig (Typ bzw. Qualität)
Ladehilfsmittel schadhaft
ausladende Last wirkt auf Ladehilfsmittel
zu geringe Bedien-/Freiräume vorhanden
Gangbreite nicht ausreichend
mangelnde Ordnung und Sauberkeit (verschüttete Ware, Gänge durch Ware und leere Paletten zugestellt
unzureichende und teilweise defekte Beleuchtung
Boden beschädigt, teilweise uneben.
Management von Schäden
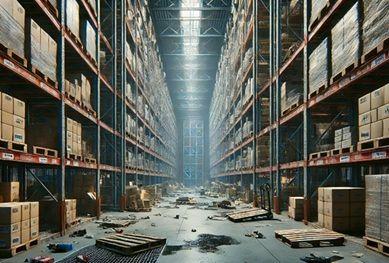
Unordnung und Gefahrenpotenzial im Hochregallager
Unordnung im Lager beeinträchtigt Arbeitsabläufe und Sicherheit. Rasche Wiederherstellung der Ordnung ist betriebsrelevant.
Ein Managementkontrollverfahren ist erforderlich, um Berichte über Regalschäden zu bewerten und um Maßnahmen zur Sicherung gefährdeter Bereiche einzuleiten. Ein sofortiger schriftlicher Bericht des Wartungspersonals ist dabei essentiell.
Zusammengefasst geht es bezüglich der statisch relevanten Aspekte bei den Inspektionen bzw. Kontrollen um die folgenden:
Schäden durch Stoßeinwirkung an irgendeinem Teil der Konstruktion, speziell Beschädigung von Stützen und Trägern;
lotrechte Regalstützen;
Zustand und Grad der Wirksamkeit sämtlicher Bauteile, insbesondere Fußplatten und Träger/Stützen- Sicherungen;
Risse in Schweißnähten oder im Grundmaterial;
Zustand des Gebäudebodens;
Lage der Lasten auf der Palette;
Position des Ladehilfsmittels auf dem Regal und auf dem Boden;
Regal ist nach der Montageanleitung gebaut.
Überprüfung auf Überlastung
Ein Träger, Kragarm oder Fachboden ist als überlastet zu erachten, wenn eine bleibende Verformung eingetreten ist oder wenn die Durchbiegung größer ist als die spezifizierte Durchbiegung. Typische Durchbiegungsgrenzwerte sind t/200 bei Palettenregalträgern und Stahlfachböden; t/100 bei Kragarmen. Diese Werte sind an die spezifischen Spezifikationen angelehnt.
Diese spezifischen und detaillierten Maßnahmen tragen entscheidend dazu bei, die Sicherheit und Funktionalität von automatisierten Hochregallagern zu gewährleisten, indem potenzielle Risiken frühzeitig identifiziert und adressiert werden.
Durchbiegung tragender Elemente prüfen
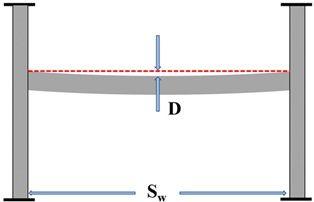
Trägerdurchbiegung (Sw Spannweite, D Durchbiegung (in der Mitte des Balkens)
Grafische Darstellung der Durchbiegung D eines Balkens über Spannweite Sw unter Belastung. Relevanz für Tragwerkssicherheit.
Im Rahmen der Wartung von Hochregallagersystemen sind bestimmte Kontrollmaßnahmen von essentieller Bedeutung, um die Sicherheit und Stabilität der Lagerstrukturen zu gewährleisten. Zwei wesentliche Aspekte, die regelmäßig überprüft werden müssen, betreffen die Sicherung der Träger sowie die Überprüfung von Lotabweichungen an Rahmenstützen.
Kontrolle der Trägersicherungen
Während Wartungs- und Reparaturarbeiten ist es entscheidend, die Trägersicherungen zu überprüfen. Dabei muss sichergestellt werden, dass alle notwendigen Sicherungsteile vorhanden sind. Fehlende Teile, die für das sichere Halten der Träger unerlässlich sind, müssen unverzüglich ersetzt werden. Dies verhindert ein unbeabsichtigtes Lösen der Träger, welches zu schwerwiegenden Sicherheitsrisiken führen kann. Um auf solche Situationen vorbereitet zu sein, sollte ein Vorrat an Träger-Sicherungsteilen stets im Betrieb vorgehalten werden.
Kontrolle von Lotabweichungen an Rahmenstützen
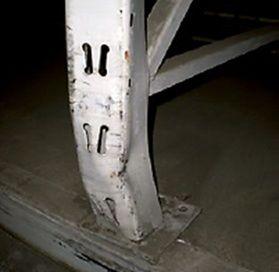
Gerissene Schweißnaht an der Fußplatte der Stütze
Die Regalstütze zeigt eine deutliche plastische Verformung. Eine sofortige Prüfung und Instandsetzung ist sicherheitsrelevant.
Die Überprüfung der Lotabweichungen an Rahmenstützen ist eine weitere kritische Maßnahme, die während der Inspektion durchgeführt werden muss. Für Regale, die unter Last stehen – dazu zählen Fachbodenregale und staplerbediente Regaleinrichtungen – darf die Lotabweichung einen Grenzwert von L/200 nicht überschreiten. Lotabweichungen, die diesen Wert übertreffen, müssen umgehend dem Lieferanten gemeldet werden, um eine Überprüfung der Bemessung zu veranlassen.
Anmerkungen zu Lotabweichungen
Spezifische Regalsysteme: Bei einigen spezialisierten Regalsystemen, wie automatischen oder Schmalgangsystemen, ist der Grenzwert für Lotabweichungen wesentlich strenger. Dies berücksichtigt die höhere Empfindlichkeit dieser Systeme gegenüber Abweichungen.
Bodenverformungen: Veränderungen des Bodens, die durch Verdichtung oder Setzung unter Belastung entstehen, müssen ebenfalls in Betracht gezogen werden. Selbst geringfügige Verformungen des Bodenfundaments können die Stabilität und Sicherheit der Lagerstrukturen beeinträchtigen.
Seitendurchbiegung bei Kragarmregalen: Bei Kragarmregalen kann die Seitendurchbiegung unter vertikaler Last die Lotabweichung erheblich beeinflussen. In solchen Fällen sollte zur Klärung weiterer Maßnahmen der Lieferant oder ein Statiker kontaktiert werden.
Seitliche Verformung mit Biegewinkel
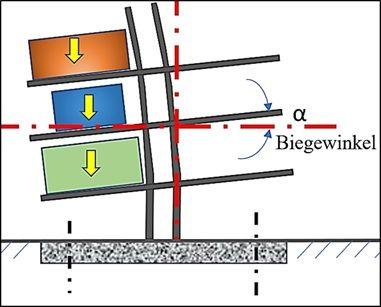
Schematische Darstellung der Biegung von Kragarmregalen
Die Darstellung zeigt eine durch Belastung verursachte Biegung mit Winkel α. Eine statische Überprüfung ist zwingend notwendig.
Diese Maßnahmen sind von entscheidender Bedeutung, um die Integrität und Funktionalität von Lagerstrukturen zu gewährleisten. Sie helfen, potenzielle Risiken frühzeitig zu identifizieren und durch proaktive Schritte die Sicherheit im Lagerbetrieb zu erhöhen.
Inspektion von Führungssystemen für Schmalgangstapler
Die Inspektion von Führungssystemen für Schmalgangstapler umfasst sowohl mechanische als auch elektrische Komponenten, die jeweils unterschiedliche Inspektionsanforderungen und -protokolle erfordern.
Mechanische Führungssysteme:
Mechanische Führungssysteme, die entweder am Boden oder an den Regalen befestigt sind, dienen dazu, die Bewegung der Schmalgangstapler entlang der Gänge zu steuern. Diese Systeme können Schienen oder physische Führungen umfassen, die eine präzise Navigation des Staplers ermöglichen und die Sicherheit durch die Reduzierung von Kollisionsrisiken erhöhen. Die Inspektion dieser Systeme ist kritisch, da jegliche Abweichung oder Abnutzung die Führungsgenauigkeit beeinträchtigen und zu Unfällen oder Beschädigungen der Lagerinfrastruktur führen kann. Solche Inspektionen sollten regelmäßig erfolgen und auf Aspekte wie physische Integrität, korrekte Befestigung und Verschleißerscheinungen fokussieren.
Elektrische Führungssysteme:
Im Gegensatz zu mechanischen Systemen nutzen elektrische Führungssysteme Technologien wie Induktionsschleifen, die in oder auf dem Boden eingelassen sind, um die Stapler zu leiten. Diese Systeme sind empfindlich gegenüber elektromagnetischen Störungen und erfordern regelmäßige Überprüfungen der elektrischen Komponenten, einschließlich der Kabel, Sensoren und der mit dem Führungssystem verbundenen Steuereinheiten. Die Inspektion dieser Systeme wird in der Regel im Rahmen der Förderzeuginspektion durchgeführt, da sie eng mit der elektrischen und elektronischen Ausrüstung des Förderzeugs verbunden sind. Hierbei wird besonders darauf geachtet, dass alle Komponenten korrekt funktionieren und keine Beschädigungen oder Verschlechterungen vorliegen, die die Funktionalität beeinträchtigen könnten.
Wichtigkeit der Inspektion:
Die regelmäßige und gründliche Inspektion sowohl der mechanischen als auch der elektrischen Führungssysteme ist entscheidend, um einen sicheren und effizienten Betrieb in Lagern und Distributionszentren zu gewährleisten. Störungen in diesen Systemen können nicht nur zu betrieblichen Unterbrechungen führen, sondern auch die Sicherheit der Mitarbeiter gefährden. Durch die Einhaltung der vorgeschriebenen Inspektionsroutinen und die frühzeitige Identifikation von potenziellen Problemen können Unternehmen kostspielige Ausfälle und Reparaturen vermeiden und die Lebensdauer ihrer Ausrüstung maximieren.
Schadensbewertung an Stützen und Aussteifungselementen
Immer wieder stoßen wir auf den Begriff Schadensbewertung. An dieser Stelle wollen wir hierzu ein Beispiel behandeln und darstellen, und zwar anhand der Regeln zur
Bewertung von Schäden am Beispiel Stützen und Aussteifungselemente.
Das Kapitel "Bewertung von Schäden am Beispiel Stützen und Aussteifungselemente" im Dokument sollte eingehend die Methoden und die Bedeutung der Schadensbewertung an Bauelementen in Lagereinrichtungen thematisieren. Dieses Kapitel kann in drei Hauptabschnitte gegliedert werden: Einführung in die Schadensbewertung, Beschreibung der Messverfahren für Schäden, und die Definition von Grenzwerten und deren Bedeutung.
Einführung in die Schadensbewertung
Zielsetzung der Schadensbewertung: Die Schadensbewertung dient dazu, die Integrität und Sicherheit von Stützstrukturen wie Stützen und Aussteifungselementen in Lagereinrichtungen zu gewährleisten. Sie hilft dabei, potenzielle Risiken zu erkennen, die die Stabilität und Sicherheit der Lagerinfrastruktur beeinträchtigen könnten.
Bedeutung der Schadensbewertung: Die Bewertung ermöglicht es, frühzeitig Maßnahmen zu ergreifen, um umfangreichere Schäden oder gar Unfälle und Zusammenbrüche zu vermeiden. Sie trägt dazu bei, die Lebensdauer der Einrichtungen zu verlängern und die Effizienz und Sicherheit des Lagerbetriebs zu erhöhen.
Beschreibung der Messverfahren für Schäden
Messung von Verformungen: Die Schadensbewertung erfolgt durch präzise Messverfahren, die bestimmen, ob die Verformungen innerhalb akzeptabler Grenzen liegen. Dabei wird ein 1,0 m langes Stahllineal verwendet, das in direktem Kontakt mit der beschädigten Stütze oder dem Aussteifungselement steht, um den Grad der Verformung zu messen. Die Messung fokussiert sich auf:
Allgemeine Knickung: Bestimmung des Zwischenraums zwischen Stütze und Lineal.
Lokale Schäden wie Beulen oder Krümmungen: Beurteilung der Schadenslänge und Anwendung anteiliger Grenzwerte.
Risse und Sprünge: Solche Schäden führen zur Empfehlung eines vollständigen Austausches der betroffenen Teile.
Spezifikation der Messpunkte: Die spezifischen Messpunkte und die Ausrichtung des Lineals werden genau definiert, um die Genauigkeit der Messung zu gewährleisten. Unterschiedliche Ausrichtungen der Stütze und des Aussteifungselements erfordern unterschiedliche Messmethoden und Grenzwerte.
Festlegung von Grenzwerten: Für verschiedene Arten von Verformungen werden spezifische Grenzwerte festgelegt:
Bei Biegung: maximal 5,0 mm Abstand zwischen Träger und Lineal.
Bei Knickung in der Ebene der Rahmenaussteifung: maximal 3,0 mm.
Bei Aussteifungselementen: maximal 10,0 mm bei einer Messlänge von 1 m.
Bedeutung der Grenzwerte
Diese Grenzwerte sind kritisch, um die strukturelle Integrität und Betriebssicherheit zu gewährleisten. Sie basieren auf Normen und Sicherheitsrichtlinien, die sicherstellen, dass auch nach einer Beschädigung eine gewisse Tragfähigkeit und Stabilität der Lagerkomponenten erhalten bleibt. Die Einhaltung dieser Grenzwerte ist entscheidend, um strukturelles Versagen zu verhindern und die Sicherheit des Personals zu gewährleisten.
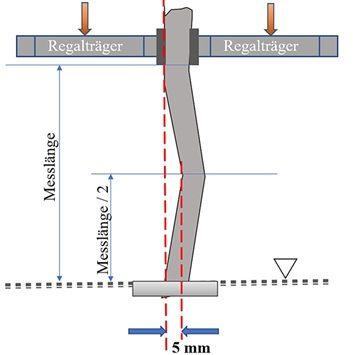
Schadensmessverfahren typischer Stützenprofile bei verstellbaren Plattenregalen
Die Abbildung zeigt eine Stützenverformung mit maximal zulässiger Abweichung von 5 mm bei halber Messlänge.
Zusammenfassend stellt dieses Kapitel nicht nur die Techniken und Methoden zur Bewertung von Schäden an Stützen und Aussteifungselementen vor, sondern betont auch die Wichtigkeit präziser Messverfahren und festgelegter Grenzwerte, um die Sicherheit und Langlebigkeit von Lagerstrukturen zu sichern.
Zeitbasierte Wartung
In der Intralogistik ist die Wartung und Instandhaltung unerlässlich, um die weit vernetzten Logistikketten aufrechtzuerhalten. Ein besonders eindrucksvolles Beispiel hierfür sind Hochregallager, die oft in beeindruckenden Höhen von bis zu 45 Metern betrieben werden. In solchen Anlagen ist die Herausforderung groß, den Überblick zu behalten, welche Komponenten gewartet werden müssen. Aufgrund des hohen Automatisierungsgrades und der Abhängigkeit der Anlagenteile voneinander ist eine umfassende Instandhaltung erforderlich. Diese umfasst nahezu alle Elemente der Anlage, von der Fördertechnik wie Rollenbahnen und Gurtförderern über automatische Belabelungs- und Packanlagen bis hin zu modernsten, hochdynamischen Regalbediengeräten.
Die Sicherheit des Personals steht bei der Instandhaltung solcher Systeme immer im Vordergrund. Die Betreiber richten sich nach dem geltenden Arbeitsschutzrecht und stellen sicher, dass alle Vorgaben und Richtlinien eingehalten werden. Dazu gehört die Anwendung von einschlägigen Normen und Richtlinien, wie der EN-Maschinenrichtlinie und der Norm EN 528, die spezifisch die Sicherheitsanforderungen für Regalbediengeräte regelt, einschließlich Aspekten wie Eingriffsschutz und Sicherheitsschalter. Diese Geräte werden im Rahmen der jährlichen Prüfungen gemäß den Bestimmungen der Betriebssicherheitsverordnung überprüft, um jegliche Gefährdungen zu vermeiden und die Sicherheit während des Betriebs zu gewährleisten.
Dieses Beispiel zeigt, wie kritisch eine systematische Wartung und regelmäßige Überprüfung aller technischen Systeme und Komponenten für die Aufrechterhaltung der Funktionalität und Sicherheit in komplexen Logistiksystemen ist. Die Einhaltung gesetzlicher Vorgaben und die sorgfältige Implementierung von Sicherheitsnormen sind dabei unerlässlich, um einen sicheren und effizienten Betrieb zu garantieren.